ATOM FlashCut FLEX SERIES
ATOM’s automated cutting systems cut with extreme precision and repeatability, to within +/- 0.1mm on most materials. We offer advanced nesting software packages that maximize yields and significantly reduce expensive material waste.
Engineered and designed to cut the hardest materials used in the petro-chemical, automotive, aerospace, composites & technical textiles, & packaging industries like compressed non asbestos, 1-2 layer steel inserted graphite, dense rubber, cross linked polyethylene foam, Kevlar, carbon fiber, plastics, and many more.
Since ATOM develops its technology in close collaboration with its clients, today it is able to offer the most advanced and most applicable cutting solution on the market – the new FlashCut ‘FLEX’.
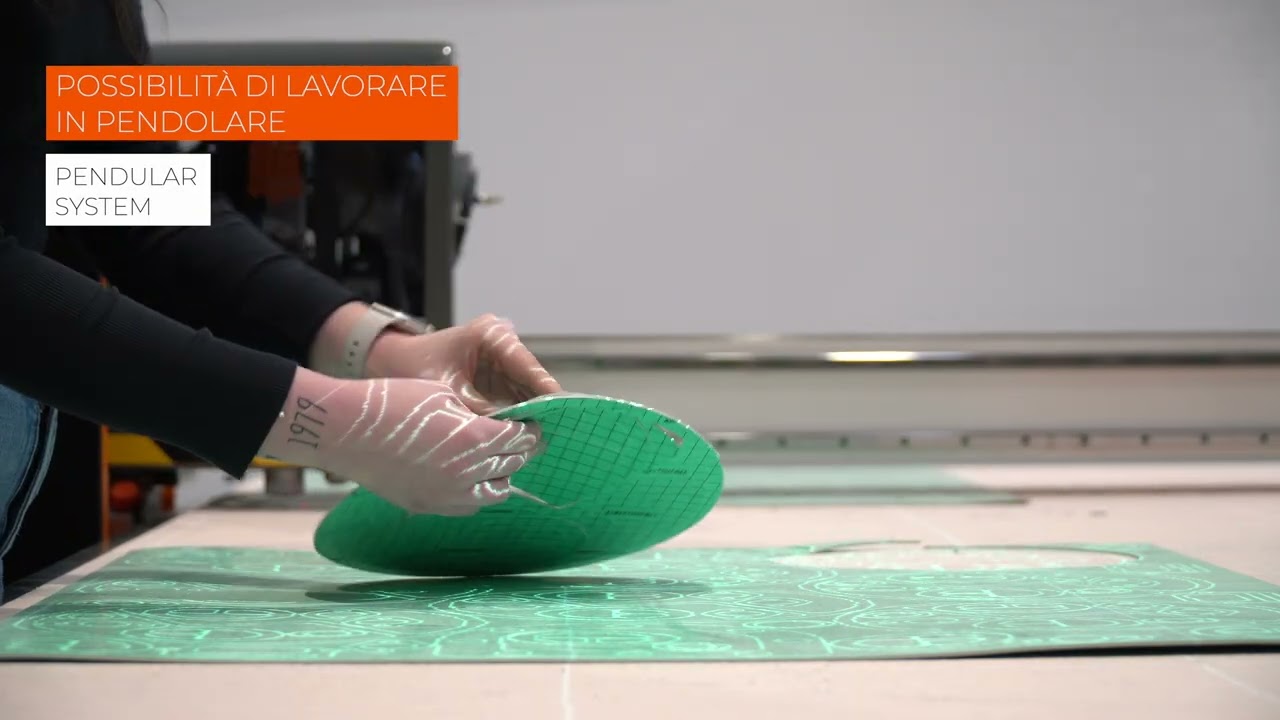
The new “FLEX” series represents the evolution of the previous architecture of great success with over 2500 units installed worldwide since 2002. The new structure boasts several improvements in technology (cutting head, tooling options, electronics) and software (interface program, CAD compatibility & options) together with the new compact design make them extremely flexible for a wide range of industrial applications.
The solid steel rack and pinion system in place of a cogged belt increase the precision and operating speeds of the machine while the two pre-charged linear guide rails and enlarged beam adds to the robustness of the system. The new cutting surface with a higher degree of planarity coupled with the unique partitioned zoned vacuum system add even more suction power improving cut quality and overall accuracy.
With the option to add an overhead camera system for material contour recognition, projectors to visualize the cutting layout for assisted parts collection, the modular multi-tool cutting head and the powerful yet simple to use production control software make the FlashCut “FLEX” an efficient, versatile and powerful CNC digital knife cutting system.
+PLUS|Flashcut Flex
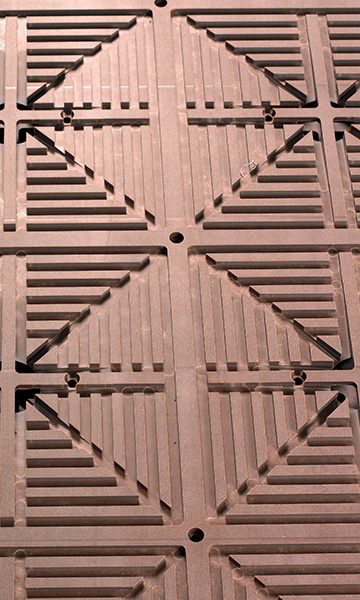
Partitioned Vacuum System
Powerful partitioned and adjustable vacuum system. Best material fixing during cutting with highest energy saving.
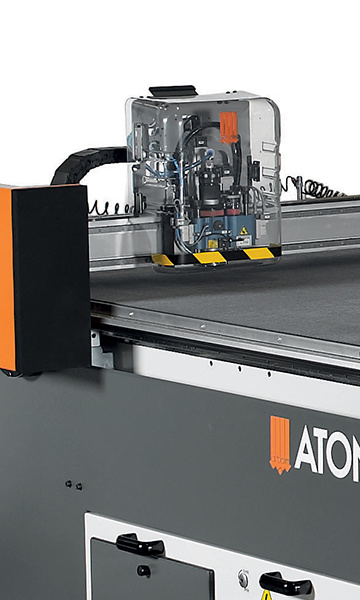
Performance and Reliability
Perfect quality and cutting speed. Precision mechanical engineering and state-of-the-art electronics.
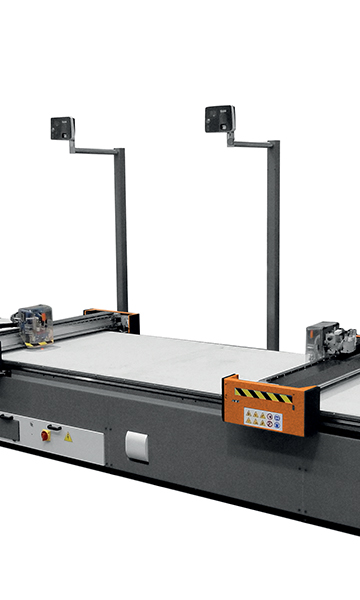
Two Cutting Heads
Two independent cutting heads to increase productivity.
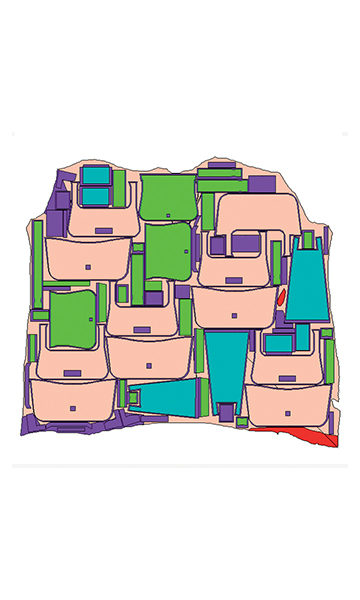
Optimized Nesting
Customized automatic nesting software. User friendly interface. Reduction of the process times and maximum material yield.
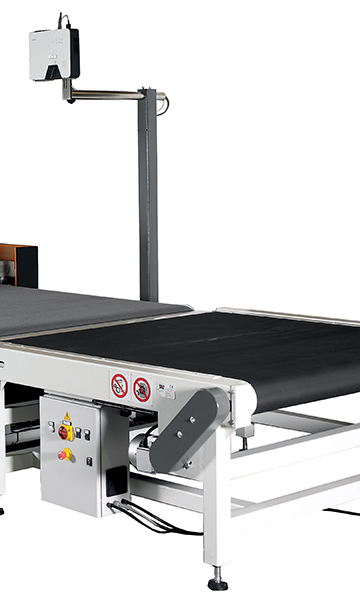
Static or Conveyorized Belt Cutting Surface
On the conveyorized models, the material feeding is carried out by the combination of the belt and two pincers mounted on the gantry.
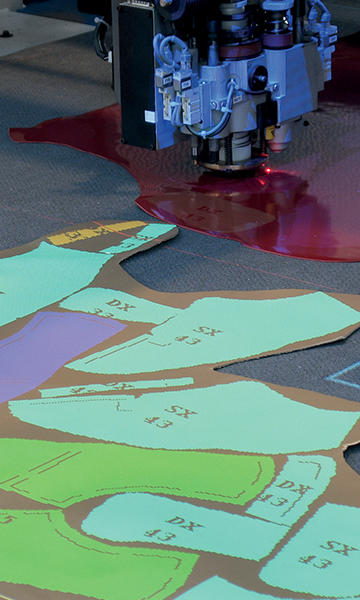
Overhead
Projectors
Optimal clarity thanks to LED lamps which offer lower maintenance and a long life.
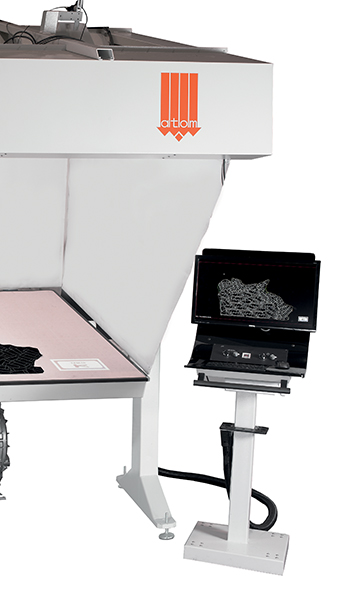
Acquisition
Systems
In-line and off-line Acquisition Systems optimize material yields and dramatically reduce the overall time for placing the shapes to be processed.
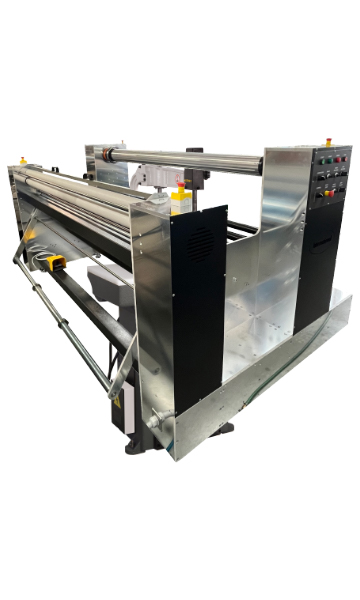
Modular Material
Handling Solutions
Standard & custom engineered material unwinds stands & winders, feeding and spreading machines, sheet-loaders, and in-line loading & off-loading tables.
Downloads
Download Flex Series Brochure
PDF - 241 KB
Download Flex 3026 B-3 Brochure
PDF - 331 KB
Download Automotive Sector
PDF - 375 KB
Download Oil and Gaskets Sectors
PDF - 654 KB