Streamlining Operations for Efficiency
Material Handling
Manufacturers Supplies Company offers a complete range of standard & custom manufactured material unwind stands & rewind stands engineered for the winding & unwinding of web based materials including gasket materials, foams & laminated foams, rubber, cork, textiles & nonwovens, paper, laminates, composites, and similar products in varying dimensions and weights.
Our unwind & rewind stands are a robust, complete, packaged solutions for unwinding web material. We source the highest quality components available, specified for your unique application, and configured for easy integration into your existing cutting or converting process.
Our unwinders & rewinders differ in terms of operation & size, can be configured for single or multiple rolls and/or web paths for flexibility, and designed to maintain the proper tension during unwinding activities prior to the cutting phase of the converting process.
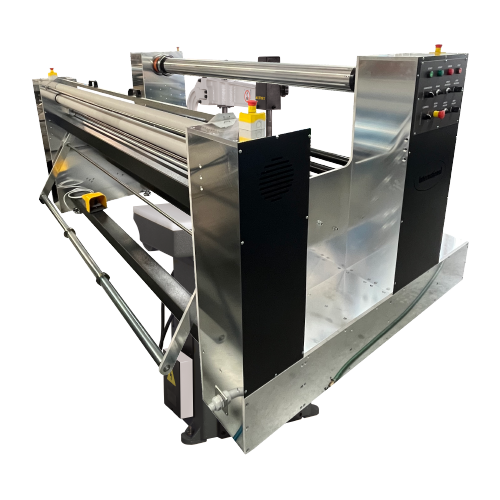
Key Features
- Maximum material width up 3,100mm
- Roll diameter to customers’ specification. Max 2500mm (Larger diameters on request)
- Roll weight up to 1500 kg (heavier rolls on request)
- Core ID: 1”, 1.5”, 2”, 3”, 4” & 6” (Special Sizes Available on Request)
- Stand-alone, or integrated with our CNC controlled die cutting or dieless cutting system
- Unwinding from a shaft with expandable chucks, or from a pneumatic expansion shaft
- Automatic edge guide control for telescopic rolls
- Driven transportation feed roller (nip roll), or direct driven unwinding shaft via motor
- Light loop-control system for nearly tension-free material supply, or pneumatic dancer arm for adjustable fabric tension
- Additional web tension control systems using load cells, ultrasonic sensors and amplifiers
- Operating speeds automatically adjusted through the CNC cutting system
- Optional slitting modules for edge trimming
- Optional secondary unwinding cradle for rolls up to 1000mm in diameter
- Optional rewinder/winder for liner removal
- Optional locking casters for ease of mobility
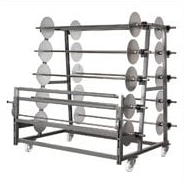
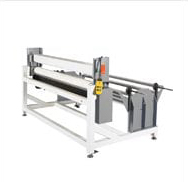
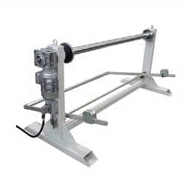
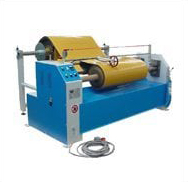
A Wide Variety of Solutions
Cradle Unwinds
The cradle unwind was developed to unwind materials that have damages or no cores. Rolls of insulation, roofing membranes, heavy rubber are examples of some of these materials. The roll of material is placed in the cradle which can consist offree rolling or powered rollers.
These rollers can be driven by a motor with control or pulled by the power of the line. The material is unrolled at little or no tension to prevent stretching of the materials. Since the rollers are surface driving the roll of material the speed will be constant in relation to the line speed.
Powered Unwinds w/ Loop Tension Control
Manufacturers Supplies Company engineers and designs completely custom shafted roll stands to suit specific unwinding applications. Powered or motorized unwind with open or closed loop tension control are suitable to unwind & rewind foam materials in large jumbo rolls with dimensions up to 2.5 meters in diameter and widths up to 2.0 meters. It is possible to install this unit in line with automated full beam die cutting presses, CNC Programmable Traveling Head Presses or conveyorized digital knife cutting systems.Our unwind stands are pre-configured for easy integration into any converting process and we have the experience to design and fabricate exactly what is needed to meet the operating specifications.
Unwind with Nip Feed-Pulling Station& Slitting System
We manufacture nip roll stations and pull roll stations that can be used to set tension zones or master line speeds. The unwinder with a nip roll feeding system is normally integrated with various automated cutting machines and “pulls” the material from an unwind roll using silicone coated nip rolls and stepper motors. This nip feed station synchronizes with the start/stop signal of the automated cutting system to allow automatic feeding of the material off the unwind stand and onto the table of the automated cutter. These stations easily synchronize with any section of the production line to help continue production at an even pace. This synchronization allows production to continue at an even pace without material tensioning related issues.
Rewinders & Rewind Stands
MSC offers a complete line of standard & custom engineers rewind stands to meet your production needs with numerous features and options to fit your specific converting requirements. Our model 94K shafted center driven rewind stand is designed to rewind rolls of paper, film and nonwoven material directly from your process on a roll to roll basis. The web tension is automatically and dynamically controlled by a closed loop load cell tension control system. Load cell transducers with closed loop feedback measure web tension directly at the web. The output of the controller maintains the correct torque required from an AC motor and AC Vector drive changing tension dynamically as the product roll is wound up. Self-closing safety chucks hold the product rolls safely and firmly in position. If the operator forgets to close the chucks they will close automatically when the product roll is turned over.
Slitting Modules
Our diverse capabilities make any type of slitting stand, station, or module possible. Integrated in-line slitting stands, trim units, drop-in retrofit modules, and even stand-alone slitter rewinders, are all available. Our slitting modules are custom engineered to the exact specifications and requirements to handle a variety of materials and can include razor, shear (blade & counter-blade) and crush cut slitting configurations.