Feba & Imesa
AUTOMATIC LOG SLITTING
FEBA Srl Converting Machinery custom engineers & manufactures a complete range of roll converting systems for the adhesive & non-adhesive tape markets, foam & rubber converters, textile manufacturers, producers of foils, protection films, laminates, graphite, roofing membranes & similar materials for over 40 years in Milan Italy.
IMESA Srl, a 40 year old Italian company, engineers & manufactures a complete range of multi-blade slitters, slitters-sheeters & transversal guillotine cutting systems, with working widths from150mm to 3200mm, for companies working in several industries including; gaskets, heavy rubber, conveyor belting, calendared materials for pipe production, expanded materials, leather, transportation upholstery and similar fields.
Their production includes fully automatic electronic lathe slitting systems (single & multi-shafted), slitters-rewinders, semi-automatic & fully automatic log winders, packaging machines, sawing machines for protection films & specialty laminating systems. FEBA also designs special machines to “keep in touch” with the new materials to convert.
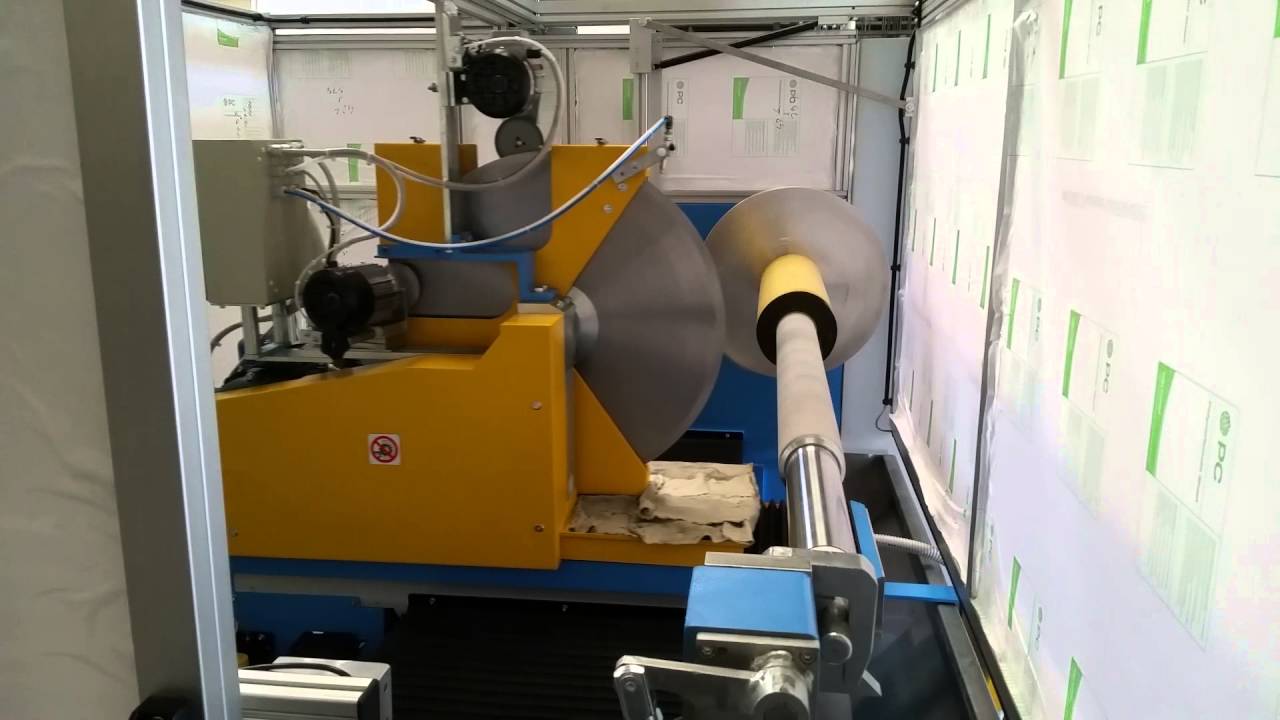
Excellent quality standards, technology, high slitting precision, versatility & custom solutions are distinctive features of the FEBA machinery range which qualify them a world leader in the converting sectors
The IMESA machinery range are commonly used for slitting & converting coated rubbers & resonated-fabrics, gum rubber, foam & laminated foams, non-asbestos materials, PTFE, silicone, SBR, PVC, nitrile, polyester, & urethane belting materials, fiberglass & Kevlar fabrics, & flexible materials in general.
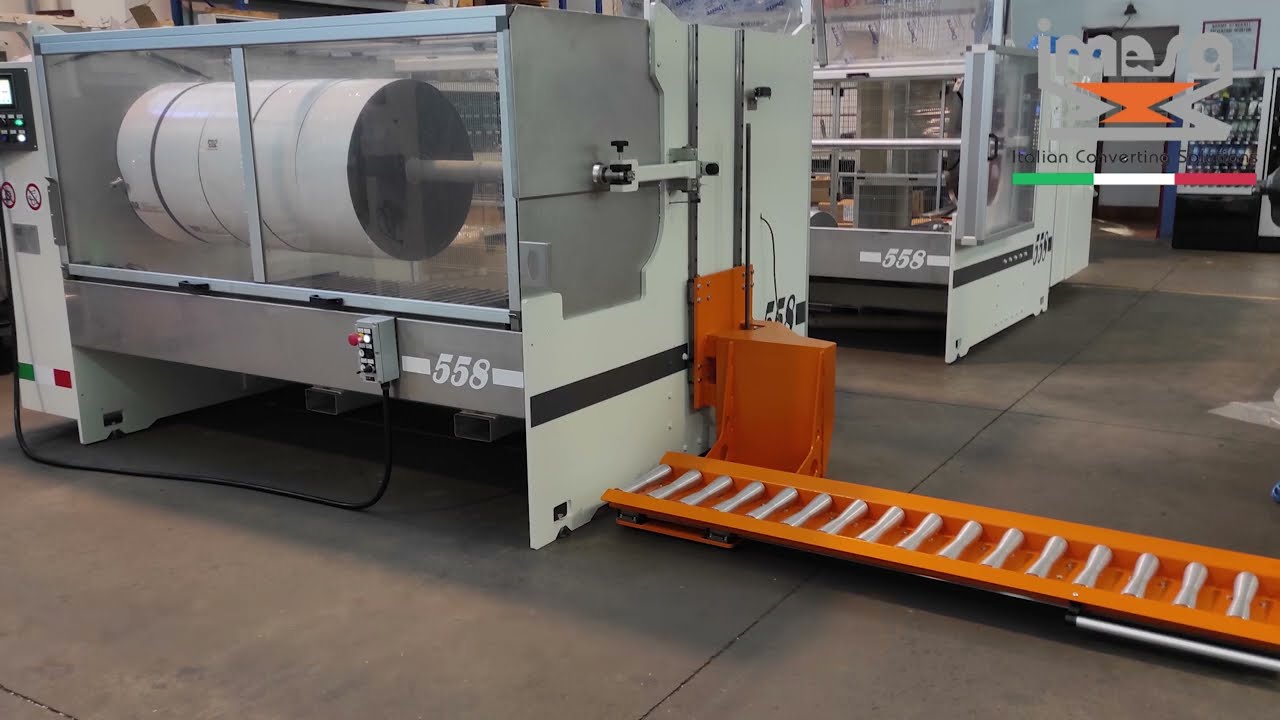
The flexibility and strength of IMESA allows them to integrate standard slitting systems with special equipment engineered & manufactured on demand indicative of the customer’s unique production requirements. All of the IMESA machinery ranges are strictly compliant with the latest European CE safety requirements and the quality as well as the reliability is guaranteed by continuous tests to which they are subjected to at the end of each manufacturing process.
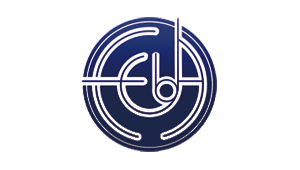
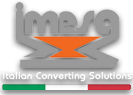