IMESA KK2
Multi-Layer Laminating Systems
The IMESA KK2 Multi-Layer Laminating System combines the same advanced features as the KK1 series but also lamination capabilities to manufacture custom composites from a wide variety of foams and other materials using hot melt films and pressure-sensitive adhesives.
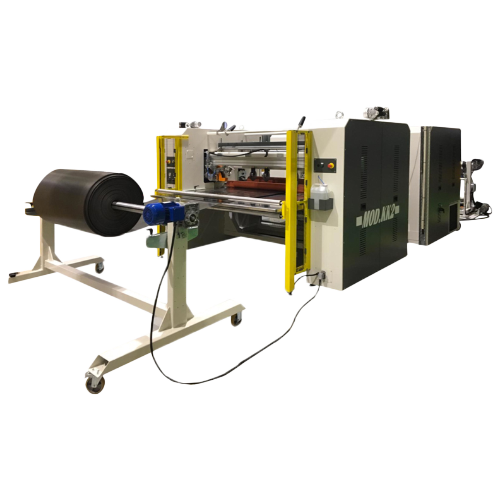
The IMESA KK2 Multi-Layer Laminating System is the ideal solution for converters that want the ability to combine multiple substrates with double sided adhesive films in a single operation. The KK2 multi-layer laminator includes the same features & general specifications as the KK1 laminating machine including slitting & sheeting capabilities but also adds multiple unwinds & rewinds to create a finished custom composite substrate. These substrates include but are not limited to open & closed cell foams, woven textiles, coated fabrics, thermoplastic films, pressure sensitive adhesives and other specialized materials. The KK2 laminating solution is customized to meet the specific converting requirements of the customer.
The KK2 multi-layer laminating system is equipped with the following features:
- Powered material unwind with loop sensor, motor & mechanical brake – Maximum diameter of 1400mm
- Automatic material web guide system with precise edge control.
- Variable operating speeds from 0 – 20 meters per minute.
- Entrance table with adjustable inclination to avoid the “curling” effect.
- Optional powered infeed conveyor system
- Infra-Red preheating station
- Upper unwind for adhesive film with mechanical brake & 3” expansion shaft.
- Lower unwind for adhesive film with mechanical brake & 3” expansion shaft.
- 1st Calendar: Upper & lower motorized silicone covered calendar rollers complete with heating device with adjustable temperature up to 300° Celsius.
- Upper & Lower rewind station with electronic clutch and 3” pneumatic expansion shafts for the removal of the adhesive liner.
- Upper unwind for 2nd material addition with mechanical brake & 3” expansion shaft.
- 2nd Calendar: Upper & lower motorized silicone covered calendar rollers complete with heating device with adjustable temperature up to 300° Celsius
- Variable calendar spacing from 2-100MM with mechanical visualization
- Adjustable air score slitting unit (blade/counter-blade or pressure cut).
- Upper & Lower rewind station with electronic clutch and 3” pneumatic expansion shafts
- Optional semi-automatic sheeting unit with rotating circular slitting blade.
- PLC Touchscreen to check the machines operating functions.
- Optional entrance & exit tables for sheet lamination.
Downloads
Download IMESA K Series Laminators Brochure
PDF - 1.00 MB
- Description
- Technical Specifications
The IMESA KK2 Multi-Layer Laminating System is the ideal solution for converters that want the ability to combine multiple substrates with double sided adhesive films in a single operation. The KK2 multi-layer laminator includes the same features & general specifications as the KK1 laminating machine including slitting & sheeting capabilities but also adds multiple unwinds & rewinds to create a finished custom composite substrate. These substrates include but are not limited to open & closed cell foams, woven textiles, coated fabrics, thermoplastic films, pressure sensitive adhesives and other specialized materials. The KK2 laminating solution is customized to meet the specific converting requirements of the customer.
The KK2 multi-layer laminating system is equipped with the following features:
- Powered material unwind with loop sensor, motor & mechanical brake – Maximum diameter of 1400mm
- Automatic material web guide system with precise edge control.
- Variable operating speeds from 0 – 20 meters per minute.
- Entrance table with adjustable inclination to avoid the “curling” effect.
- Optional powered infeed conveyor system
- Infra-Red preheating station
- Upper unwind for adhesive film with mechanical brake & 3” expansion shaft.
- Lower unwind for adhesive film with mechanical brake & 3” expansion shaft.
- 1st Calendar: Upper & lower motorized silicone covered calendar rollers complete with heating device with adjustable temperature up to 300° Celsius.
- Upper & Lower rewind station with electronic clutch and 3” pneumatic expansion shafts for the removal of the adhesive liner.
- Upper unwind for 2nd material addition with mechanical brake & 3” expansion shaft.
- 2nd Calendar: Upper & lower motorized silicone covered calendar rollers complete with heating device with adjustable temperature up to 300° Celsius
- Variable calendar spacing from 2-100MM with mechanical visualization
- Adjustable air score slitting unit (blade/counter-blade or pressure cut).
- Upper & Lower rewind station with electronic clutch and 3” pneumatic expansion shafts
- Optional semi-automatic sheeting unit with rotating circular slitting blade.
- PLC Touchscreen to check the machines operating functions.
- Optional entrance & exit tables for sheet lamination.
Benefits of Adhesive Based Lamination
Adhesive-based fabric-to-foam lamination reduces cost and improves product quality in the manufacture of upholstery, automotive interiors, acoustical wallboards, carpet, shoes and office furniture.
- Meet environmental regulations by eliminating flame lamination.
- Increase overall line speeds and throughput.
- Precisely control the exact volume of adhesive applied.
- Use non-foam materials such as breathable films and nonwovens.
Imesa Laminator Configurations for Acoustic & Thermal Insulated Panels, Interiors, Gaskets & Technical Components
- Automotive
- Aerospace
- Insulation
- Flooring/Roofing
Imesa Model KK1 T LC TC F: Hot oil double side laminator, with slitting and continuous cross cutting unit and external rewinder. This machine can laminate material (foam, felt and similar) with thermal adhesive/foil and standard PSA. The lamination calendar is composed of an upper and lower fluoropolymer covered steel roller, with a thermal oil heating system, adjustable up to 445 F..
The longitudinal slitting system is specifically designed for thick foam materials up to 150mm in thickness. The system works with 360mm powered circular knives cutting on a squared nylon counterblade. The automatic transversal cross cutting device can sheet the material at different speeds and at different set lengths, “following” the material… the system has a “double trim” option, to get a (clean) cut on the first and the last edge of the sheets.
Imesa Model K1 DS TC Belt: Double side laminator with entrance feeding conveyor, transversal cross cutting unit and two exit rewinders. This laminator is suitable to laminate stretchy material (such as EPDM foams) in both rolls or sheets thanks to the entrance conveyor belt checked by a brushless motor with adjustable inclination to avoid the curling effect. When laminating sheets, the FTC sheet presence sensor detects the first edge of the sheet allowing the Laminator to transversally cut between the two sheets even when the top surface is laminated.
Imesa Model KK1 DS LC 2 REW: Double sided laminator equipped with a powered unwind, two large diameter calendars, with slitting and external double axis rewinder. This laminating system is ideal to laminate foam and sponge materials (even thick), due to the double calender and the large diameter of the nip rollers (250mm OD). After the slitting station we have a double option for the upper rewinder: |Rewinder| remove a liner from the final product (to rewind the roll without wrinkles), or |Unwinder| laminate the material with another liner or foil. The dual external rewinder can rewind two rolls at 1000mm or a single roll at 1500mm.
Imesa Model KK1 DS LC Pre-cut: Double sided laminator with powered unwind, slitting unit and two exit rewinders. The external unwind is equipped with an AC motor + inverter, dancer bar for loop control and an automatic web guide with +/- 50mm stroke. This laminator has a Pre-cut device capable of cutting the liner (and not the adhesive) and the ability to insert a “tabbing option” between liner and adhesive (similar to an overlap liner). The score cut slitting unit cuts with pressure on a powered steel countershaft, with a minimum slitting width of 25mm and maximum material thickness at 10mm.