ATOM FlashCut
Speedy B Series
The ATOM FlashCut SPEEDY B Series high production knife cutting systems are the optimal automated dieless cutting solution for the footwear and leather goods industries.
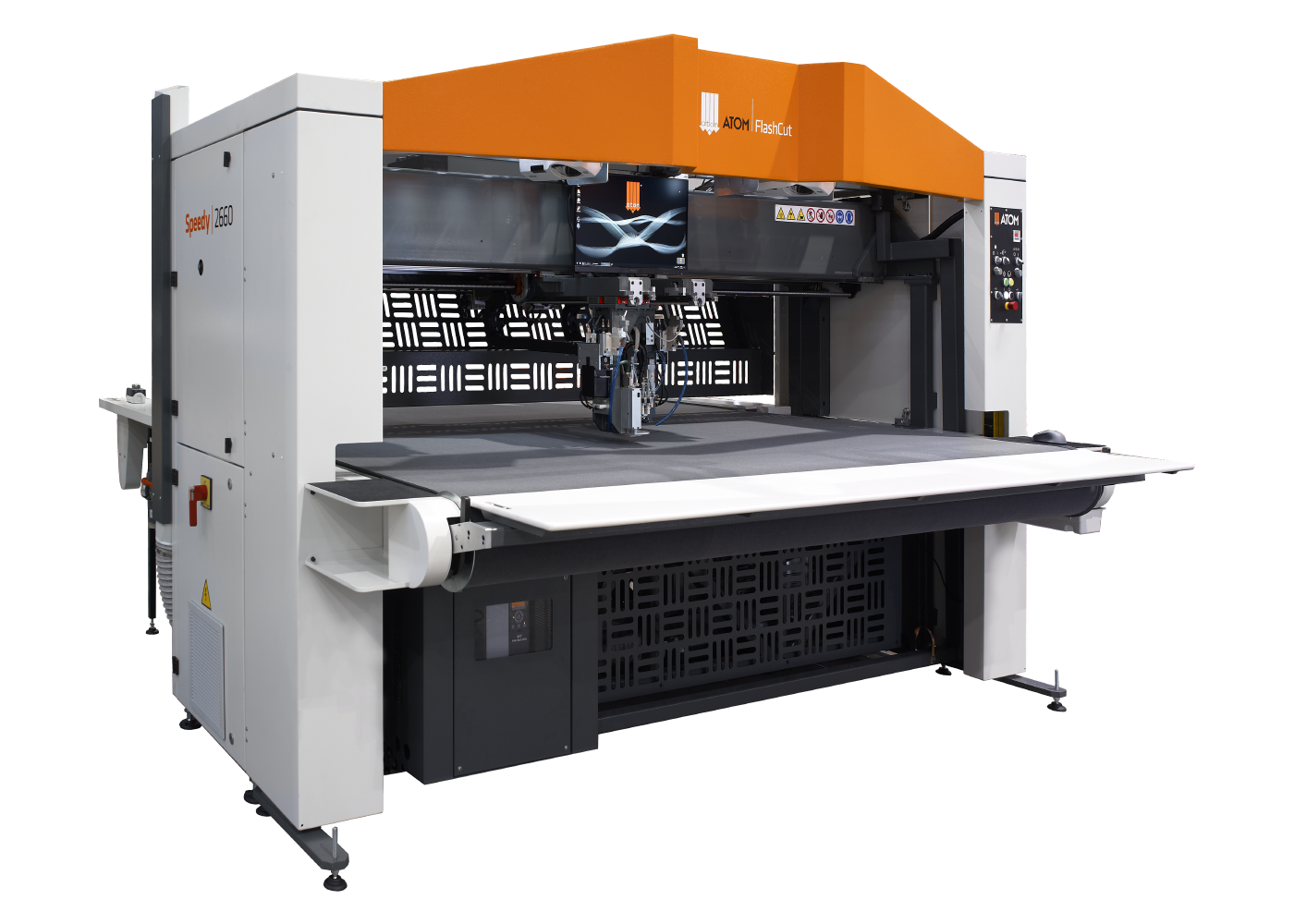
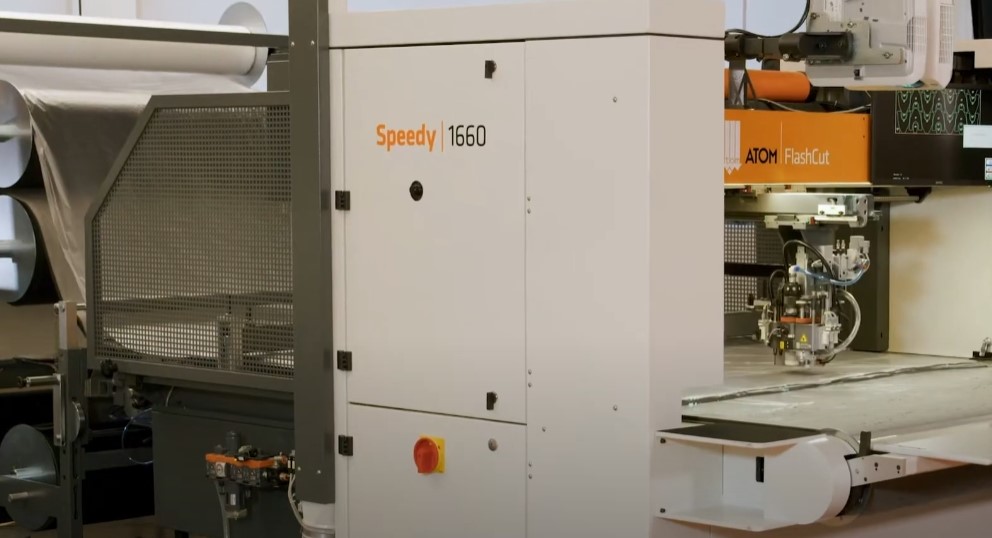
Range - Models
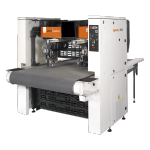
SPEEDY 1660
Working Area (MM)
1540 x ∞
Max Absorption (KW)
10,5
Sizes(MM)
2240x2828x2082
Description
With double cutting heads equipped with 5 or 7 tools and 1600mm wide conveyor belt.
Speedy 1660 Floorplan
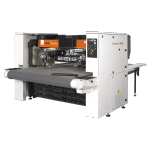
SPEEDY 2160
Working Area (MM)
2040 x ∞
Max Absorption (KW)
12,9
Sizes(MM)
2734x2853x2264
Description
Same design and features of 1660 models, but with a 2100mm wide conveyor belt.
Speedy 2160 Floorplan
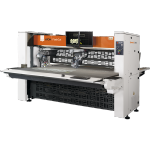
SPEEDY 2660
Working Area (MM)
2535 x ∞
Max Absorption (KW)
20.2
Sizes(MM)
3220x3170x2302
Description
With 2600mm wide conveyor belt and tilting table to increase the support and nesting area.
Speedy 2660 Floorplan
Modular Heads
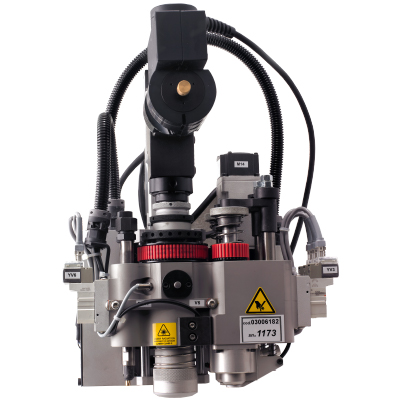
5-Tool Head
The 5-tool cutting head increases the overall versatility of the ATOM Flashcut and is one of the key factor of its success - the ability to total cut, score cut (partial depth cut) & kiss cut with one module, two auxiliary stations that can be equipped with rotating punches for precise small diameter holes, a creaser wheel or kiss cutting knife, a 4th station that includes a marking pen to apply part #’s and trademarks and a 5th non-rotating punch station that is used on light-weight materials. With this versatile head, the Flashcut now becomes a multi-functional production system for a variety of market sectors.
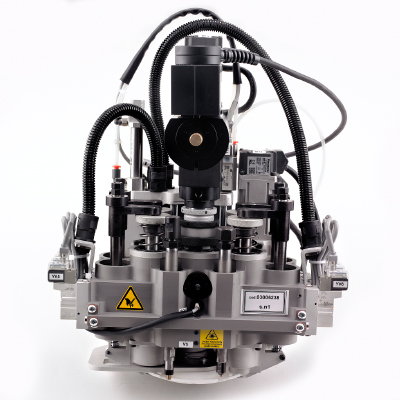
7-Tool Head
The 7-Tool head offers the same combination as the 5-Tool head yet adds two additional rotating punching-drilling stations for increased flexibility. The pneumatically controlled belt-driven punch stations are primarily used for perforating leather, or for punching small diameter holes in gaskets & textile materials. Four independent punch tools on a single head allows for different hole sizes to be produced on the same job. To accommodate different applications, punches are available in sizes ranging from 0.5mm to 8mm & are made from tungsten carbide or high-speed steel (HSS).
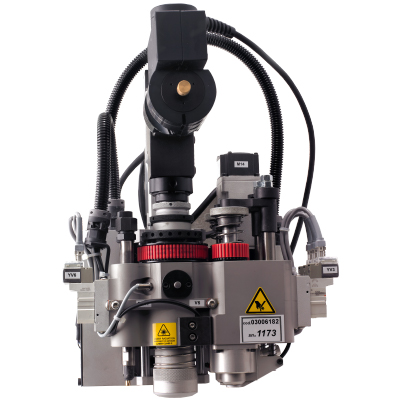
5-Tool Head
The 5-tool cutting head increases the overall versatility of the ATOM Flashcut and is one of the key factor of its success - the ability to total cut, score cut (partial depth cut) & kiss cut with one module, two auxiliary stations that can be equipped with rotating punches for precise small diameter holes, a creaser wheel or kiss cutting knife, a 4th station that includes a marking pen to apply part #’s and trademarks and a 5th non-rotating punch station that is used on light-weight materials. With this versatile head, the Flashcut now becomes a multi-functional production system for a variety of market sectors.
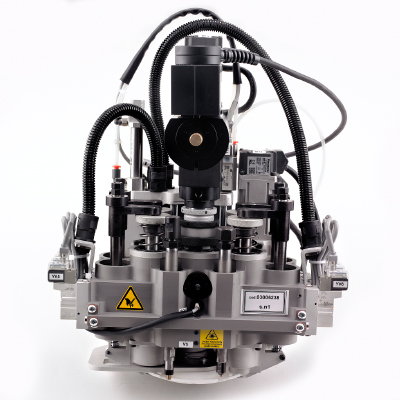
7-Tool Head
The 7-Tool head offers the same combination as the 5-Tool head yet adds two additional rotating punching-drilling stations for increased flexibility. The pneumatically controlled belt-driven punch stations are primarily used for perforating leather, or for punching small diameter holes in gaskets & textile materials. Four independent punch tools on a single head allows for different hole sizes to be produced on the same job. To accommodate different applications, punches are available in sizes ranging from 0.5mm to 8mm & are made from tungsten carbide or high-speed steel (HSS).
Tooling Combinations
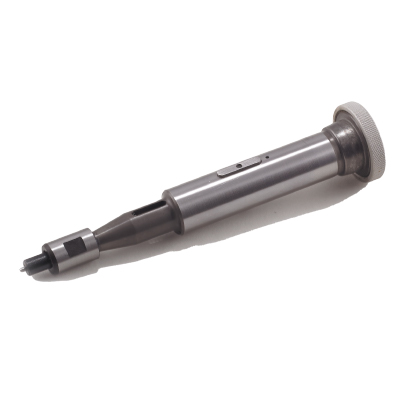
Side auxiliary tools can include rotating punches/drilling stations, kiss cut tool, creaser wheel for carton stock or thin plastics, or a 45° angle knife. Only available on the 5-Tool or 7-Tool modular head.
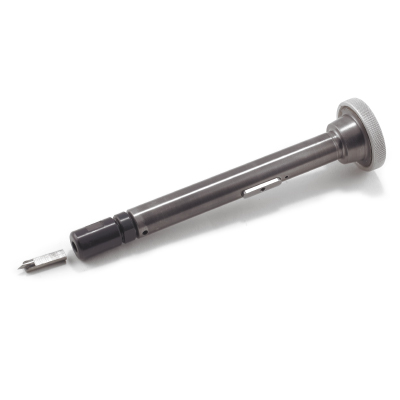
Side auxiliary tools can include rotating punches/drilling stations, kiss cut tool, creaser wheel for carton stock or thin plastics, or a 45° angle knife. Only available on the 5-Tool or 7-Tool modular head.
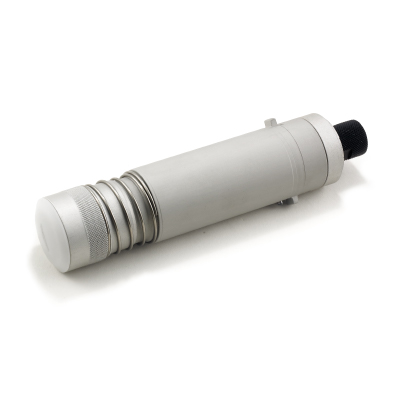
The Drag Knife Chuck (DKC) is ideal for total cutting rigid materials like thin compressed non-asbestos, laminates & plastics up to 6mm (1/4”) in thickness.
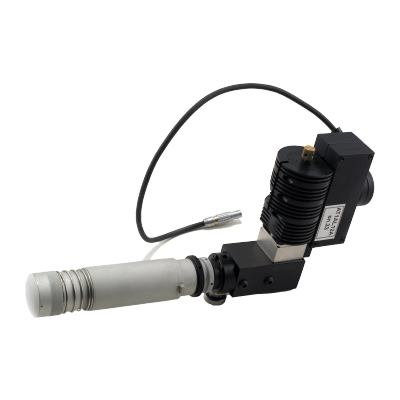
The Electric Oscillating Knife Chuck (EOK), is ideal for cutting softer, low-medium density materials like thin foams, soft rubber, pure graphite, leather, laminates, adhesives and similar products.
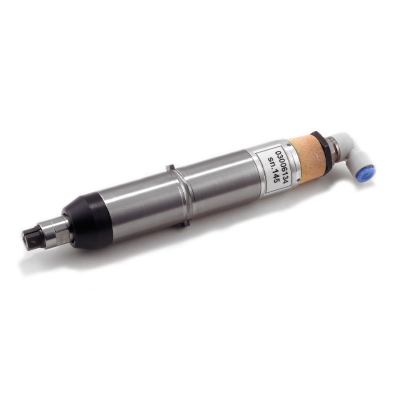
The pneumatic milling chuck, or PMC, was designed for companies that want the flexibility for light-duty milling applications for rigid materials, primarily plastics (ABS, UHMW, PP, PE etc..), that are not capable of being cut with the traditional pneumatic oscillating knife chuck.
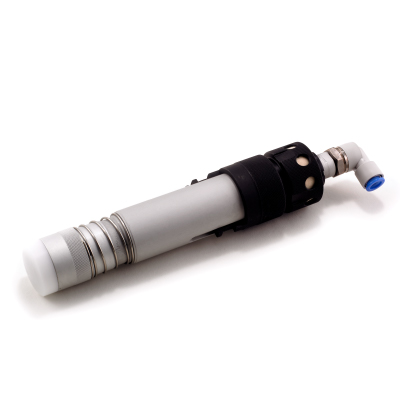
The Pneumatic Oscillating Chuck (POC), is an air driven tool engineered for cutting the most difficult materials but is also used for cutting thick, soft substrates as well.
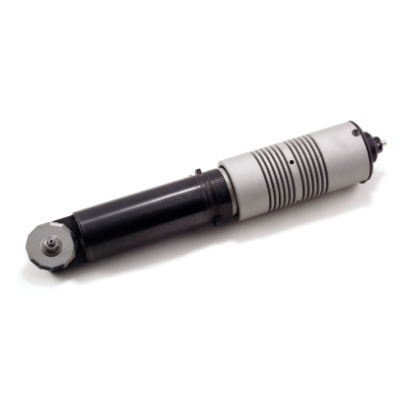
The Powered Rotary Chuck (PRC), is designed for cutting difficult fibrous materials, both uni-lateral & bi-lateral weaves, at a high rate of speed. The PRC is suitable for processing carbon fibers, Kevlar, fiber-glass, aramid and technical textiles & composites in general.
Material Handling Solutions
International Unwinders-Rewinders
PDF - 720 KB
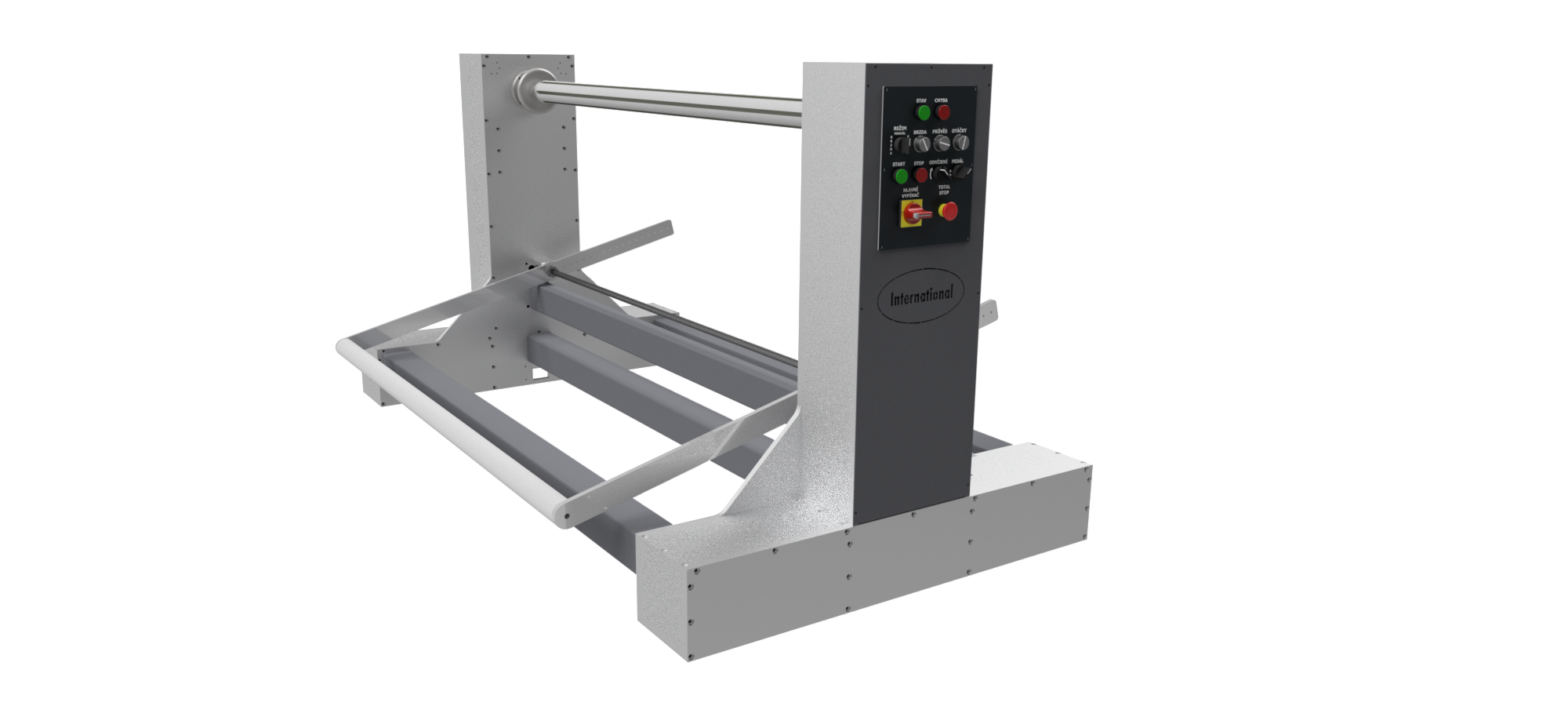
The machine is equipped with:
Dancer: A sensor for monitoring material sag, controlling the drive shaft based on its data. Winding with sag allows for reduced stretching during material uptake
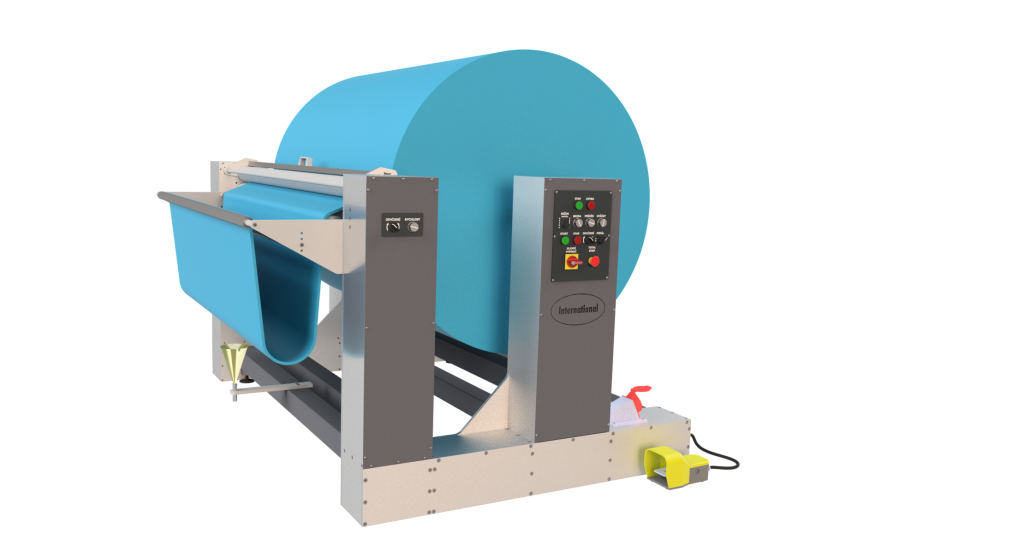
The machine is equipped with:
Puller: Assists the drive during winding and creates tension between subsequent machines and the unwinder.
Sensor: Monitors material sag, adjusting winding speed accordingly
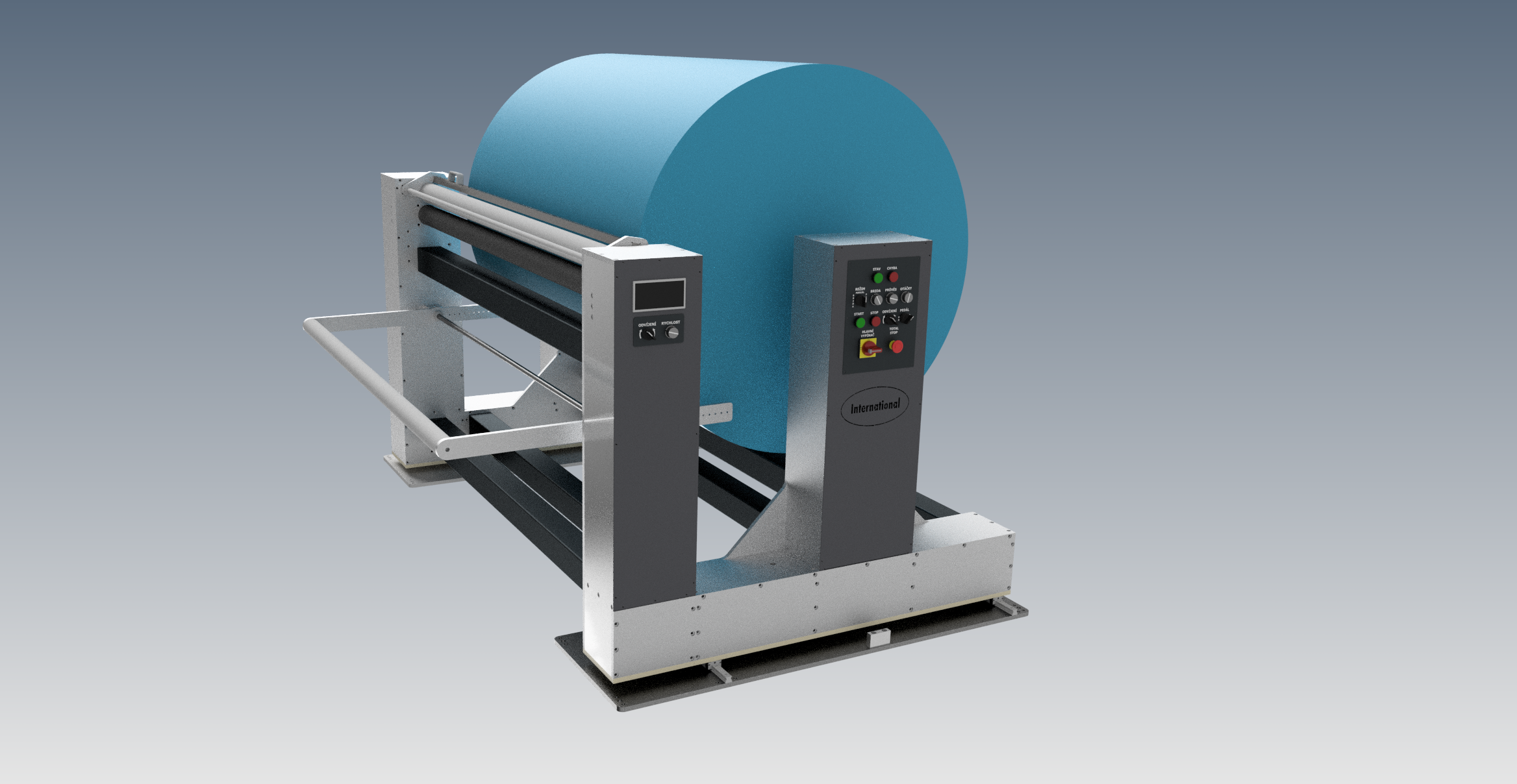
The machine is equipped with:
Dancer: A sensor for monitoring material sag, facilitating reduced stretching during material uptake.
Puller: Assists the drive during winding and creates tension between subsequent machines and the unwinder.
Side Control: A device for aligning winding; it adjusts the position lightly if the material is unwound off-center.
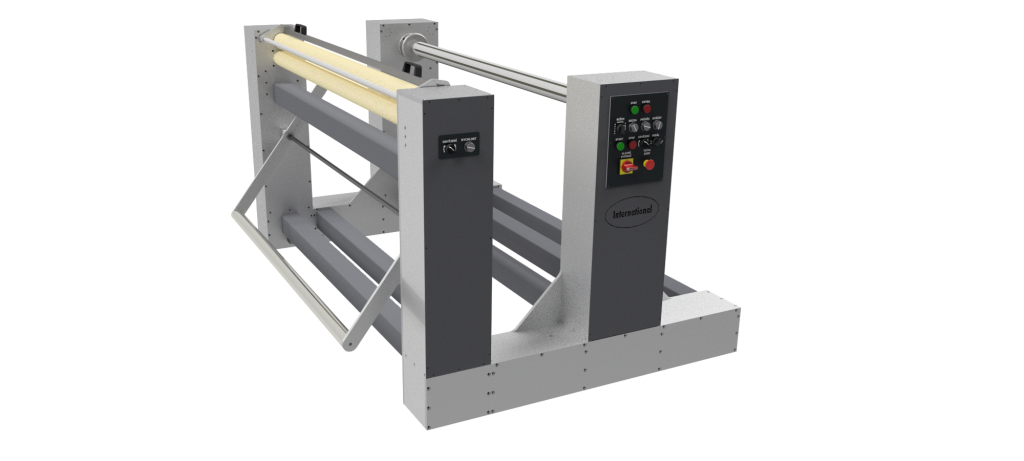
The machine is equipped with:
Dancer: A sensor for monitoring material sag, optimizing drive shaft control for reduced stretching during material uptake.
Puller: Assists the drive during winding and creates tension between subsequent machines and the unwinder
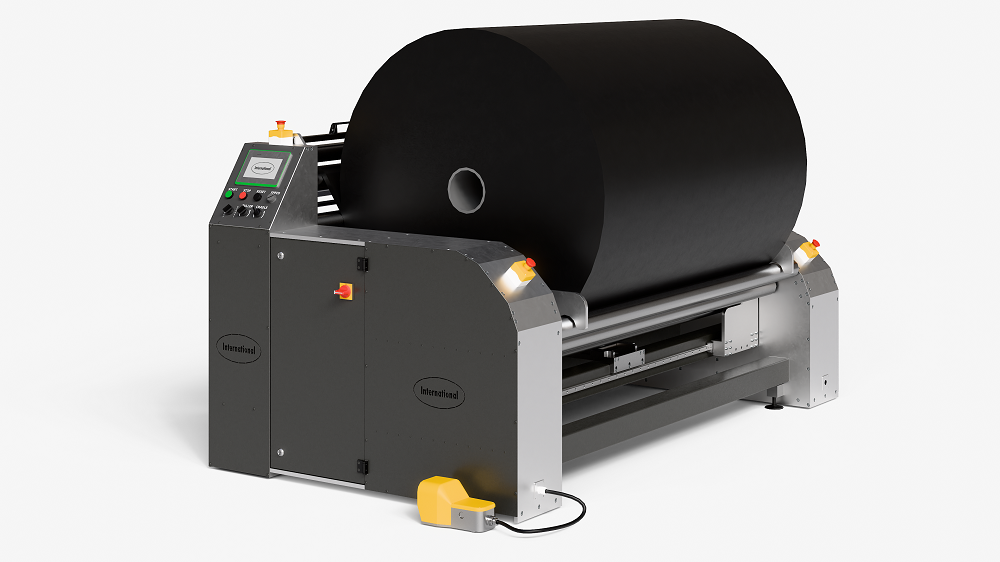
The machine is equipped with:
Dancer: For sag monitoring and optimized drive puller, ensuring reduced material stretching during uptake.
Puller: Assists the drive during winding.
Side Control: Ensures precise winding alignment, adjusting position if material is unwound off-center.
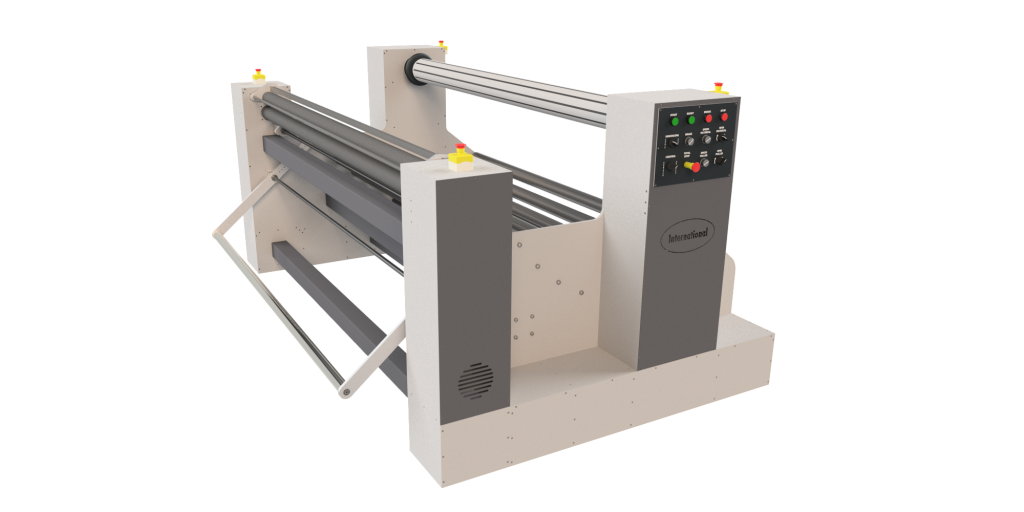
The machine is equipped with:
Dancer: For sag monitoring and optimized drive shaft control, minimizing material stretching during uptake.
Puller: Assists the drive during winding.
Side Control: For accurate winding alignment, making slight adjustments if material is unwound off-center
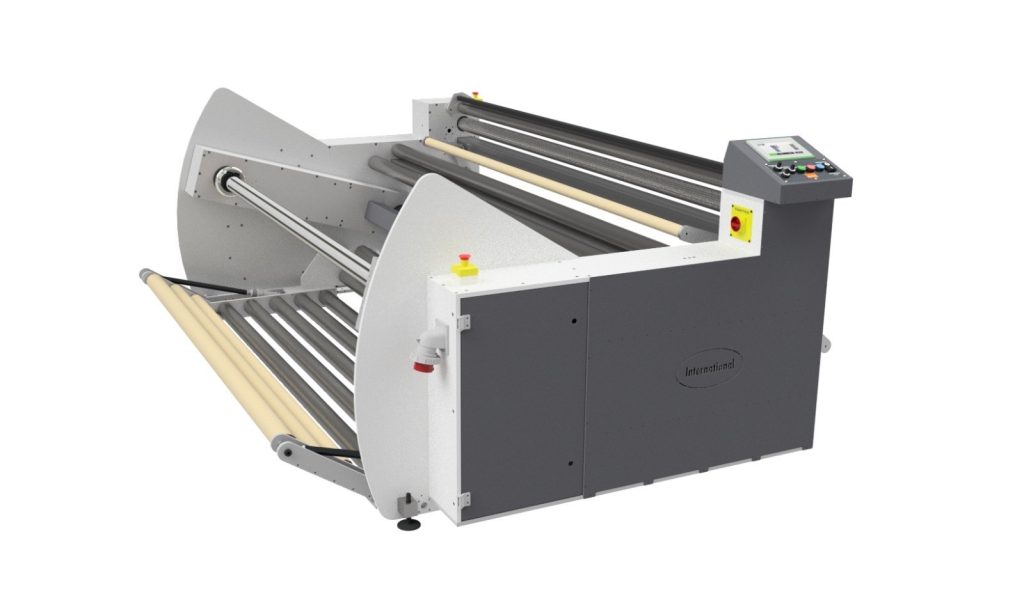
The machine is equipped with:
Loader: A device for enhanced material handling, automatically raised by the machine for improved efficiency.
Puller: Assists the drive during winding
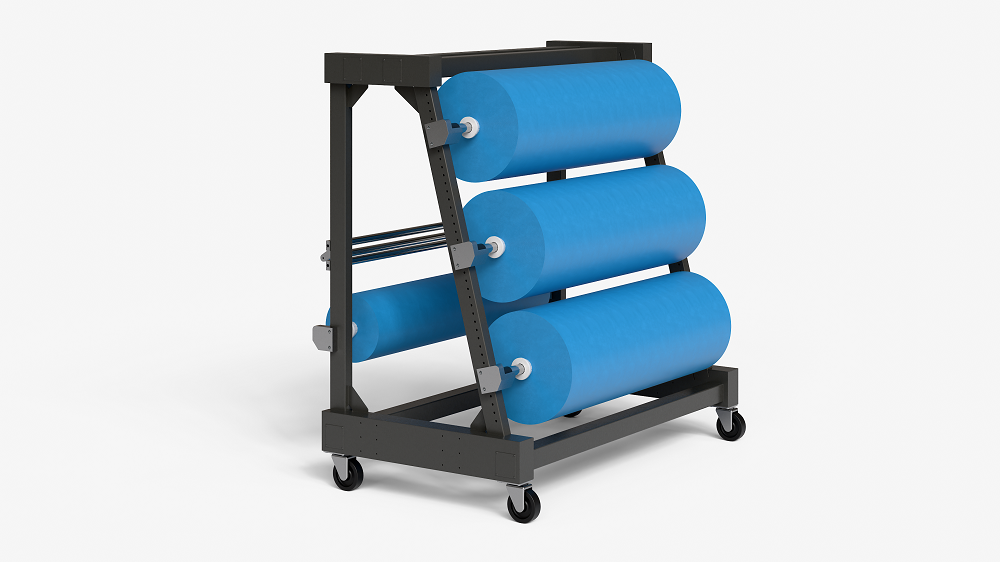
The machine is equipped with:
Holder: A device for shaft retention, with a maximum capacity of 4 units.
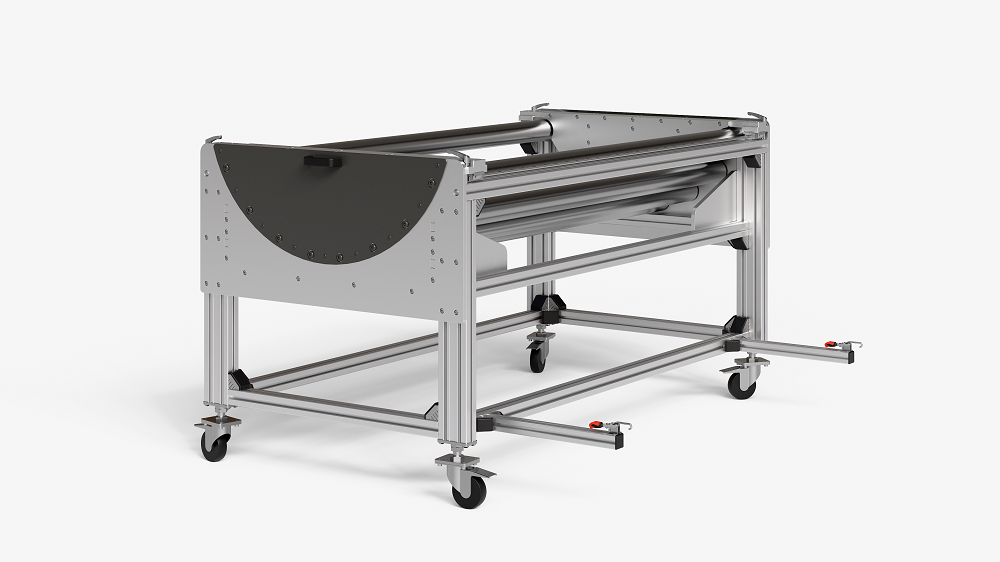
+PLUS|Flashcut Speedy
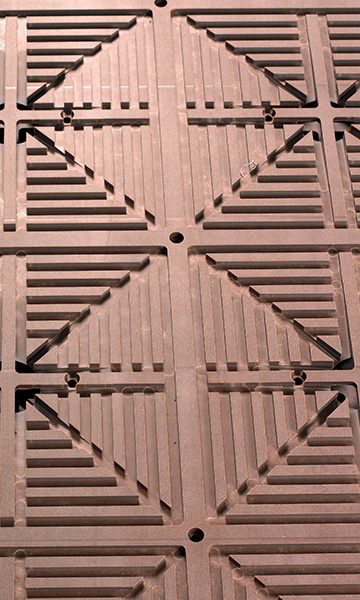
Partitioned Vacuum System
Powerful, partitioned and adjustable vacuum system. Best fixing during cutting and highest energy saving.
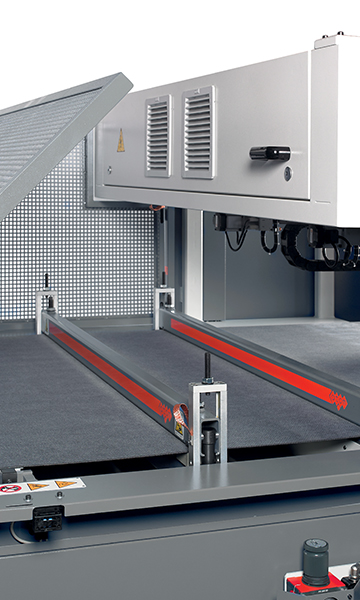
Pinch-Grab Feeding System
Covered by international patent, it assures maximum material feeding, even for multiple layers.
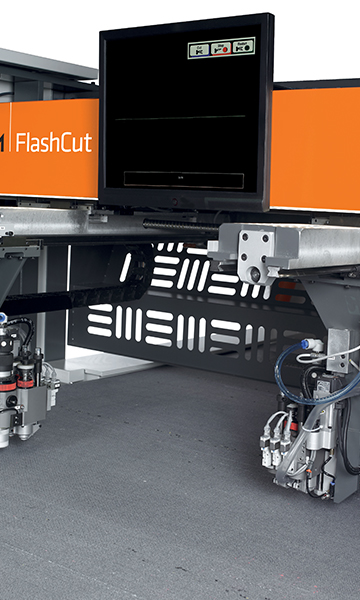
Two Cutting Heads
The cutting and punching speed, applied to two independent heads, allows high output.
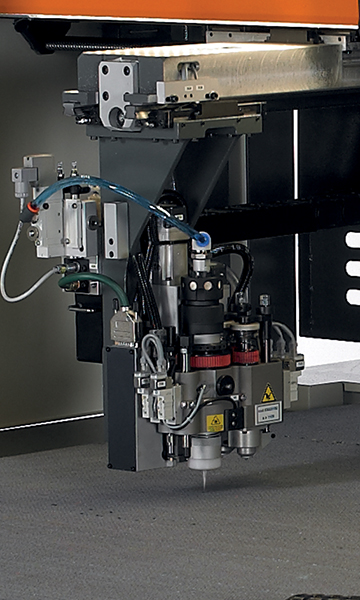
High Cutting Accuracy
The perfect parallelism between knife and working surface grants the highest cutting accuracy.
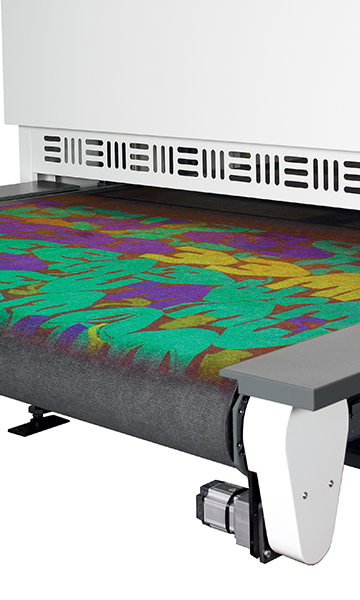
Picking Assistance
Speedy and easy picking of cut pieces thanks to the original software managing the back projectors, allowing to gather parts by size and color.
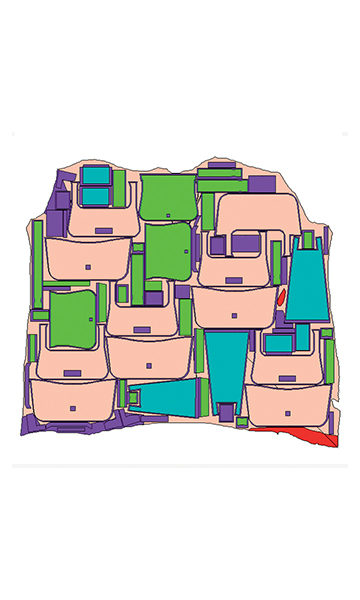
Optimized Nesting
Customized automatic nesting software. User friendly interface. Reduction of the process times and maximum material yield.
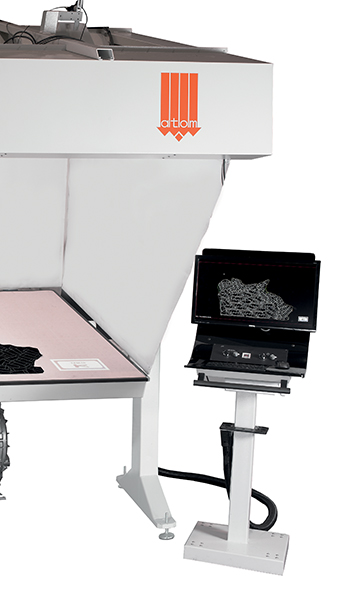
Acquisition Systems
In-line and off-line leather acquisition systems. Digital pen for marking quality areas.
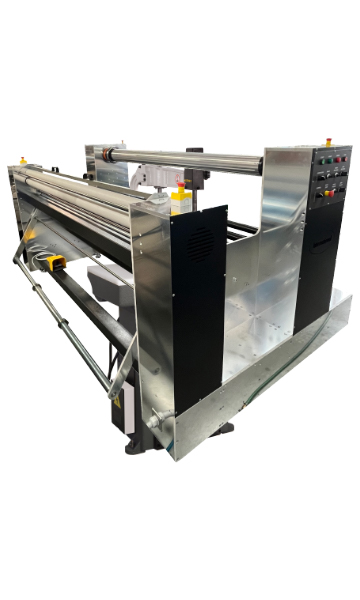
Modular Material
Handling Solutions
Standard & custom engineered material unwinds stands & winders, feeding and spreading machines, sheet-loaders, and in-line loading & off-loading tables.
Downloads
Download SPEEDY Series Brochure
PDF - 1.79 MB
Download SPEEDY 1660 B and 2160 B Brochure
PDF - 1.91 MB
Download SPEEDY 2660 B Brochure
PDF - 2.20 MB