The Chiesa F1 EDI CNC Traveling Head Press incorporates and electrically servo driven cutting head without the use of hydraulics. This ‘GREEN’ technology reduces power consumption up to 50%, eliminates all the maintenance associated with hydraulic components, and improves overall accuracy, repeatability & production throughout. In addition, to improve overall productivity & material yields, the press is equipped with either a 4 or 14 position automatic tool changing device.
Points of Strength
EDI 'FAST' Technology - Servo Driven Cutting Head
- Eliminates all maintenance associated with a hydraulic press.
- Extremely accurate cutting depth (+/- 0.01mm) – Kiss cutting capabilities.
- Noiseless operation (No pumps and motors)
- Energy efficient (Up to 50% reduction of direct costs in energy consumption)
- ‘FAST’ Technology increases production throughput up to 35%.
Material Feeding Systems
- Cutting Belt + Feeding Clamps
Suitable to cut any type of synthetic material both in rolls and sheets, loaded both from the front or back of die cutting press; the material is moved and fixed by three independent clamps. One clamp is mobile and supports the belt in the movement of the material to grant the maximum positioning of the material(s) even for soft, elastic products, cut in single or multiple ply.
- Automatic Sheet Loading
The material is loaded onto a hydraulic platform, both in single or stapled multiple layers. A special vacuum suction cup device grips the material and positions it onto the back of the machine. The feeding system will automatically stop the machine when there is no longer material available. The sheet feed system is available on all models equipped with the cutting belt & clamps. The system can also be equipped with an automatic part unloading device.
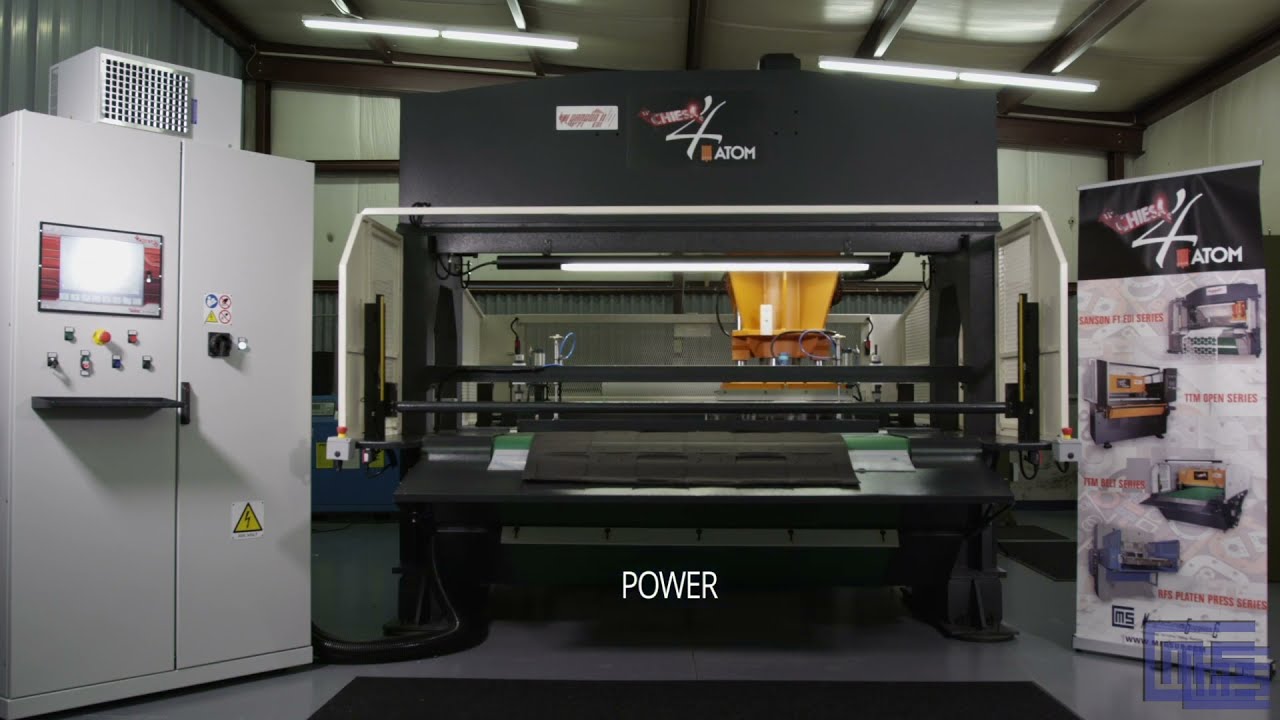
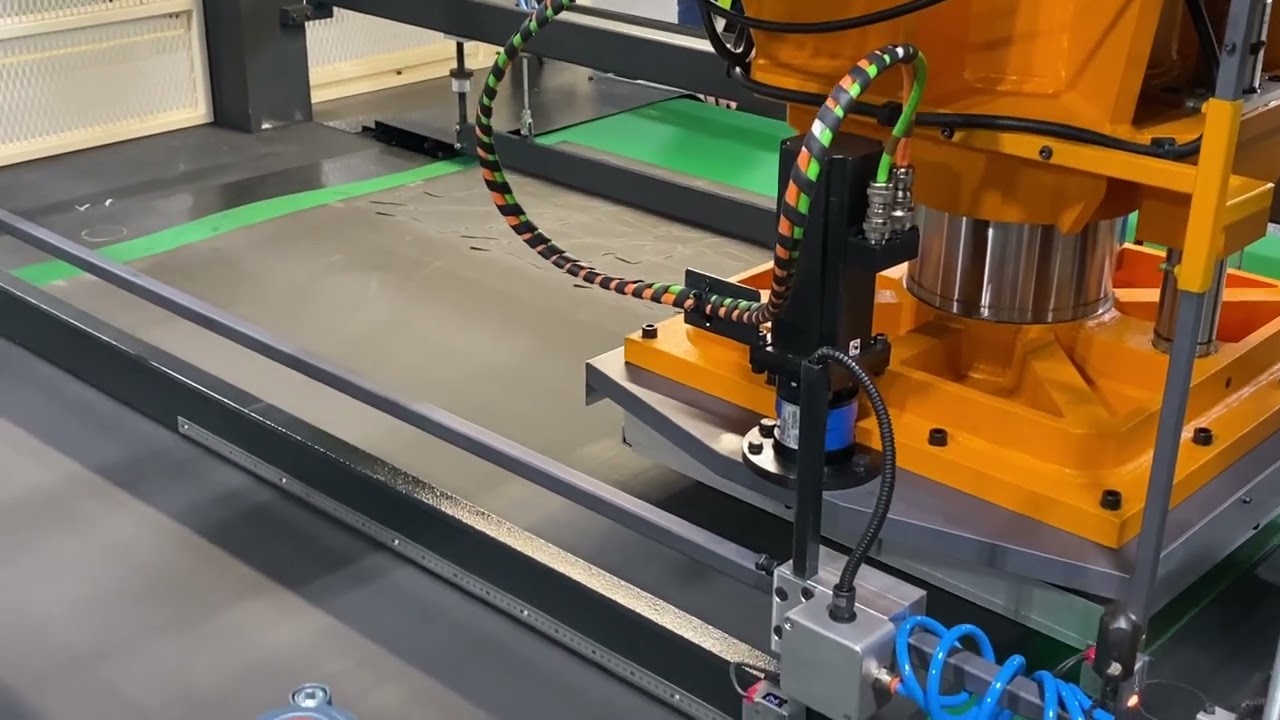
Vacuum Shuttle - Bolster Box Assembly
Automatic Pad Shifting Device
Pit-Stop Automatic Tool Changing Device
The ‘Pit-Stop’ is an automatic tool changing device mounted on the side of the press and available in a 4, 7, or 14 positions based on the type and height of the tools. The ‘Pit-Stop’ was specifically designed to increase material utilization and reduce the die changeover time. The bespoke advanced nesting software can nest multiple shapes within a roll/sheet or ‘shapes within shapes’ utilizing a single cavity tool.
Robotic Picking System
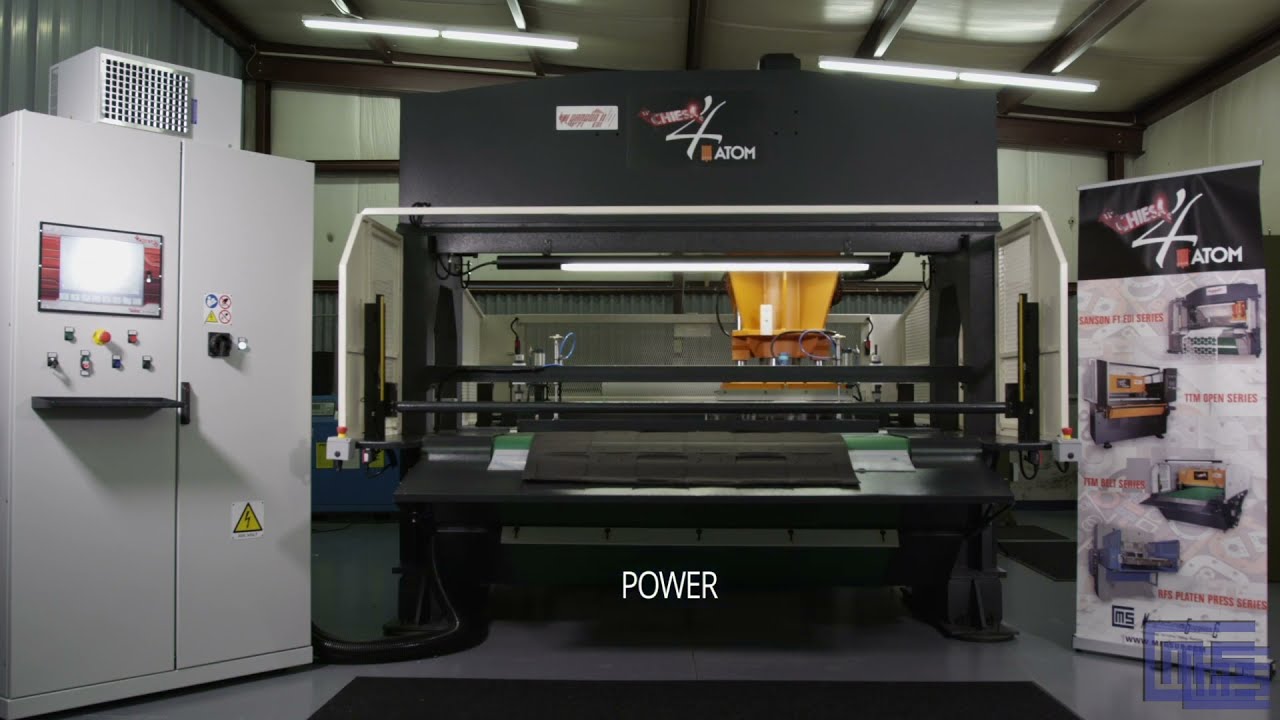
Chiesa pioneered automatic die cutting and developed the first belt fed die cutting press in the late 1980’s & patented the electrically driven (no hydraulics) CNC automatic cutting press in 2006. They are considered the market leader for industrial die cutting applications – particularly for the abrasive, gasket & automotive sectors. The long experience gained in the automatic cutting industry through thousands of installations and the steady dialog with our customers helped in creating a reliable, safe, user-friendly performing product.
These die cutting systems are extremely efficient. The robust structure and the quality of mechanical components allow cutting speeds beyond 100 punches per minute, with a precision of a few hundredth of a millimeter, which allows parts to be kept as close as possible, increasing the material savings & cutting belt life.
The cutting power, up to 110 tons, is kept steady even for extremely long production runs allowing these machines to cut hard materials of high thickness, in single or multiple layers, and use multiple dies or dies with long blade development.
Advanced Nesting software
The software allows to calculate, with considerable precision, for each material consumption and time required (thus labor cost) in order to make accurate simulations of the cutting cost, enabling better production planning and more precise offers to customers. To calculate the best material optimization it is possible to use both a DXF file and a pattern obtained via die digitization. A powerful nesting algorithm quickly & precisely calculates the best possible cutting layout using either a single shape or multiple shapes.
Once the best material optimization is obtained, the graphic image of the result is displayed on the systems touchscreen monitor along with the data relating to the cost of an individual piece or the entire run, the production time, the yield etc. The cutting programs can be transferred to the press either manually (by drive) or automatically via serial connection.
Once the best material optimization is obtained, the graphic image of the result is displayed on the systems touchscreen monitor along with the data relating to the cost of an individual piece or the entire run, the production time, the yield etc.. The cutting programs can be transferred to the press either manually (by drive) or automatically via serial connection.
Unrivalled
Algorithms
The nesting software gives the best material utilization and the fastest cutting speeds available on today’s market. Ultimate job flexibility is achieved without the need to change your current production methods. All nesting features are completely automatic. You can nest any shape-regular or irregular, into sheets or rolls and sheets joined into rolls. You can nest a breakdown of different shapes, sizes and quantities in a single run-optimizing material utilization. Bias or diagonal cutting is a standard feature. Precise job costing and timings may be calculated instantly. In this way your material ordering and stock level can be tightly controlled and kept down to a minimum.
Die
Digitization
It is possible to digitize quickly and easily the dies in order to have them ready for automatic nesting. The digitization solves any problem of die centering and positioning on the support plate. When nesting irregular shapes, a special die digitizer is used to transfer the cutting tool pattern into the computer memory in a few seconds with an accuracy of 0.1mm. The profiles of the cutting tools are memorized in the system and no further adjustments are required when nesting or cutting. Special constraints of directionality, coupling or cutting sequences can be specified by the operator. Just select with a mouse the tools and materials and then type the number of pieces you need to cut.
ATOM Flashnest
Advanced Nesting Software
For over 25 years, ATOM manufactured a complete range of CNC die cutting presses and systems with advanced, powerful nesting software packages tailored for specific markets & applications. When ATOM & CHIESA joined forces in 2012 to offer an even wider range of CNC traveling head presses, they teamed their software personnel to create a conversion software, INTELLI-CONVERTER, which will allow existing ATOM customer’s the ability to use their current layouts & shape files on their new CHIESA CNC Die Cutting Press and will also allow them to continue using the nesting software that they have grown accustomed to over the years.
Downloads
Download F1 with Robots Layout
PDF - 500 KB