Chiesa
Automation - F1 EDI Knockout & Stacking System
Chiesa Artorige, the pioneers behind automatic CNC die cutting, and the innovators of the EDI servo driven automatic cutting press, has developed & patented a new technology utilizing matched metal (male/female) tooling for processing a variety of substrates in wide web formats. This unique die cutting solution offers die cutters & converters the ability to process their materials in the original wide web format eliminating the costly & time consuming step of slitting the material down to a narrow width roll or sheet thus increasing material utilization significantly.
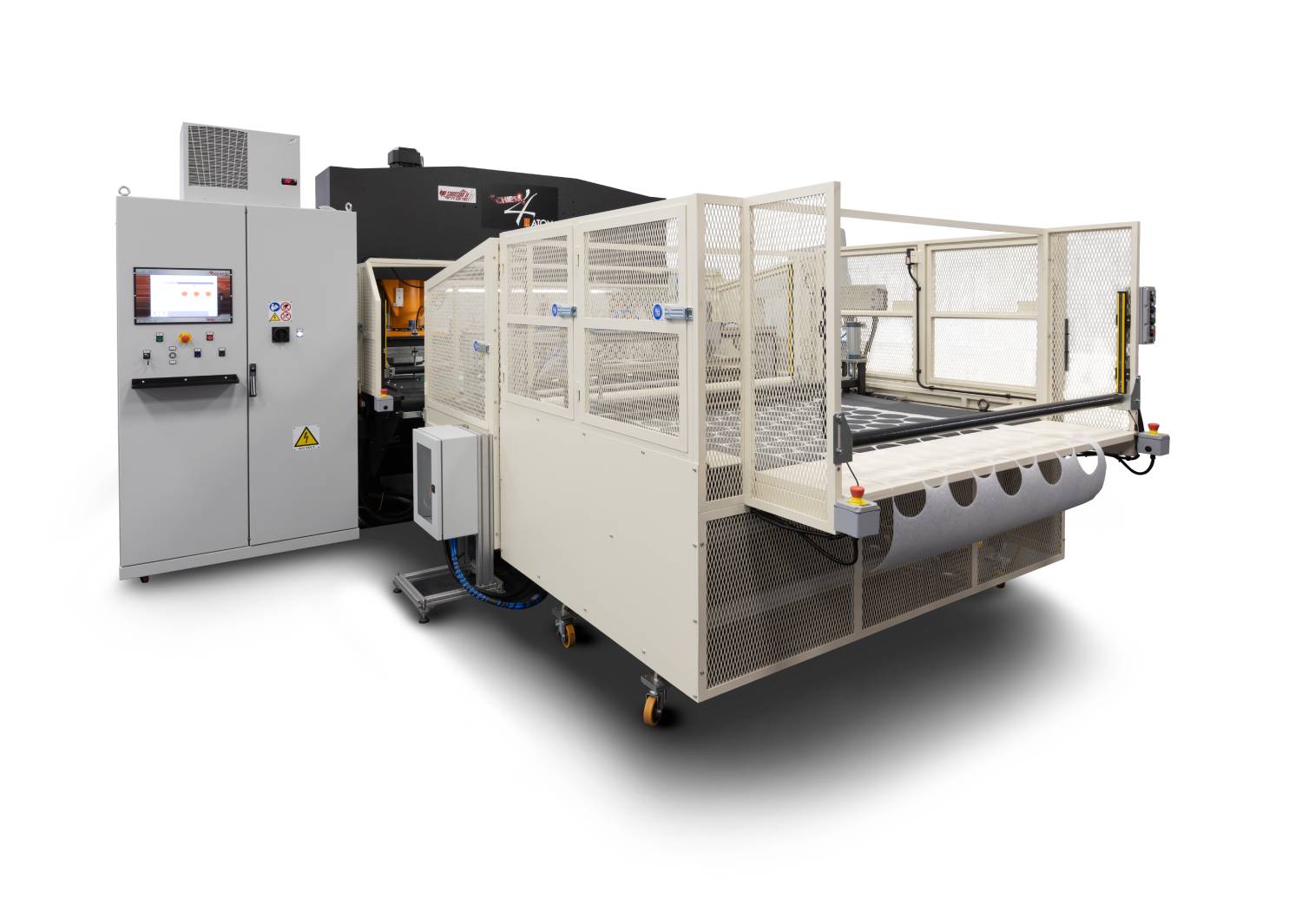
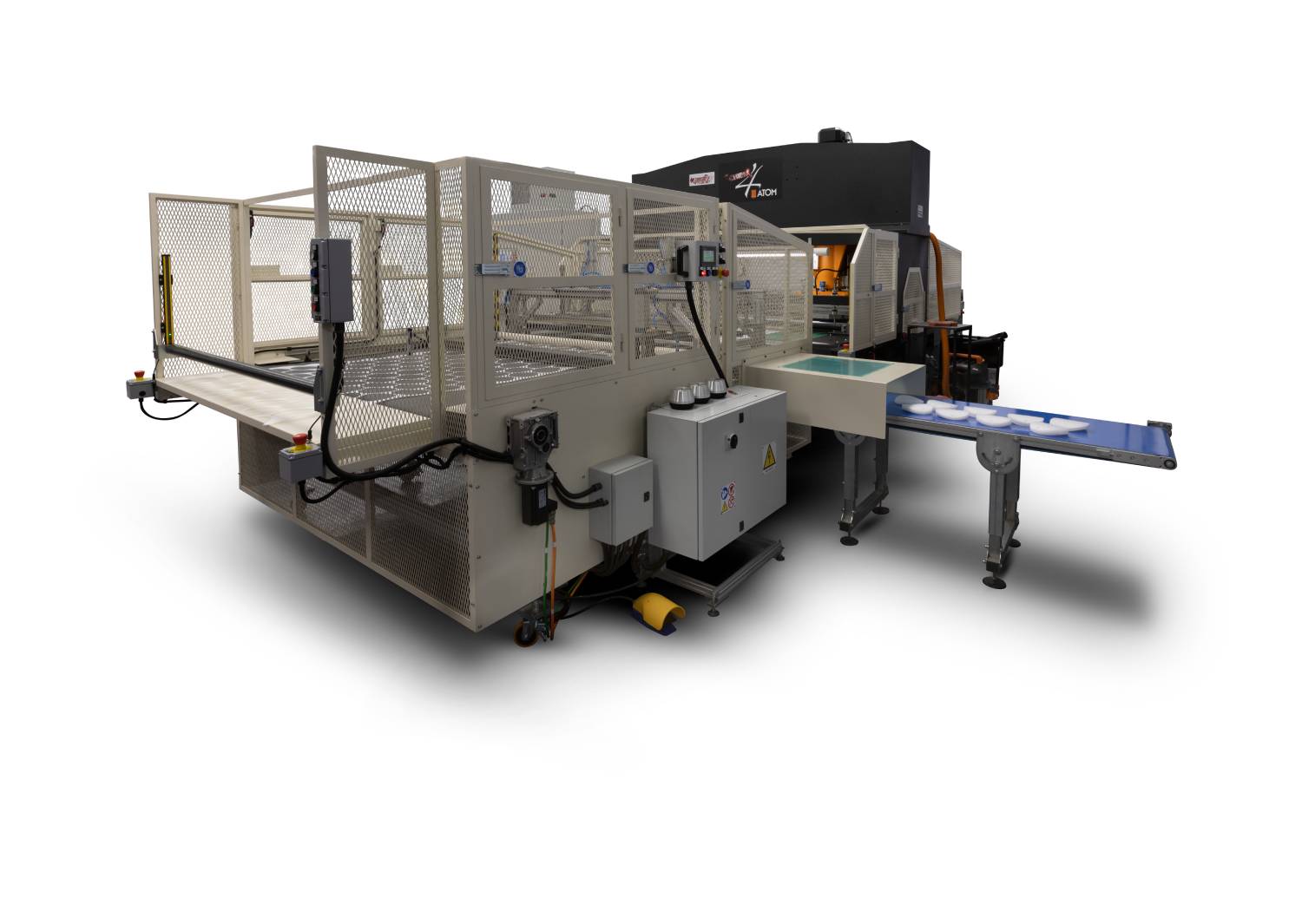
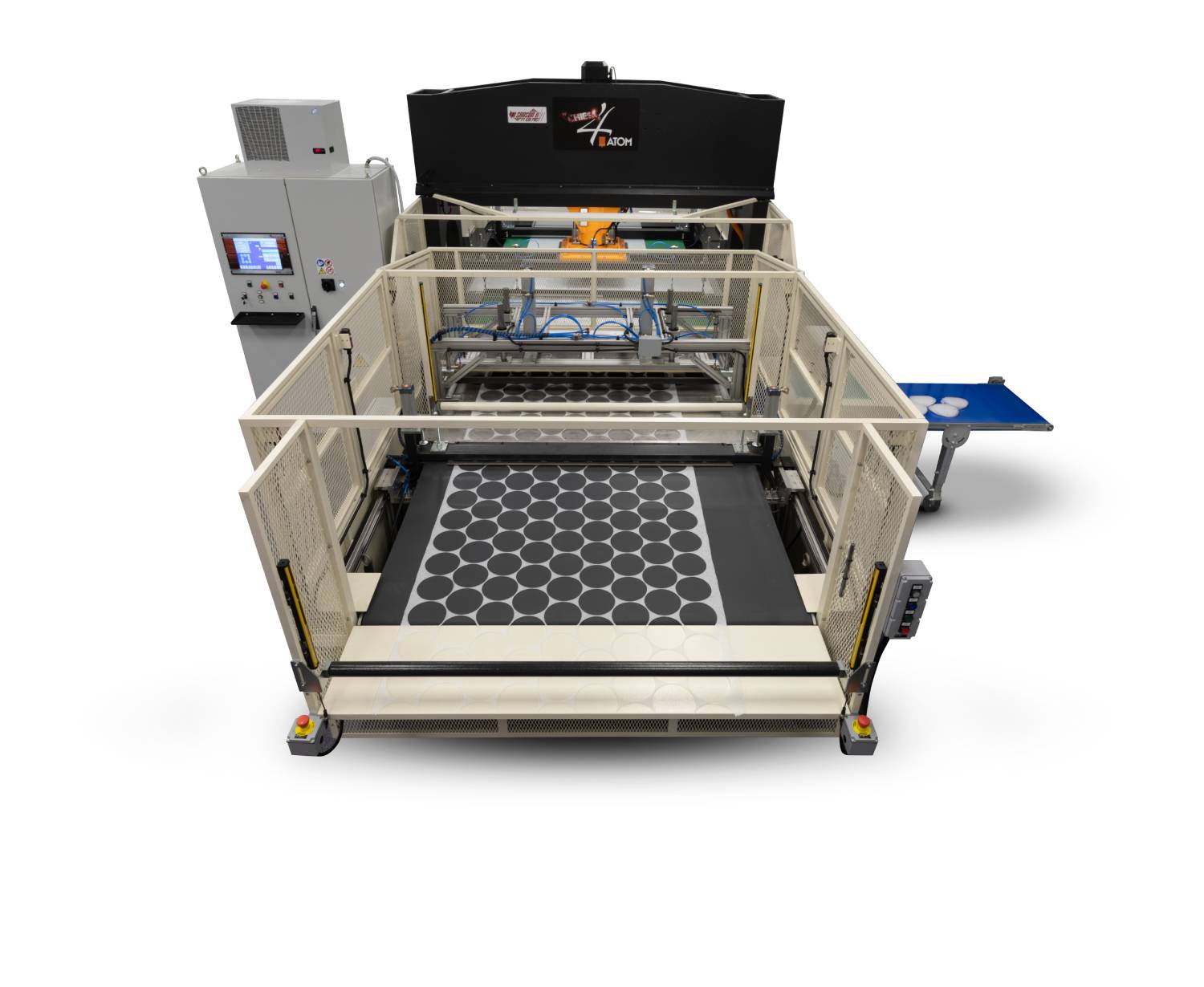
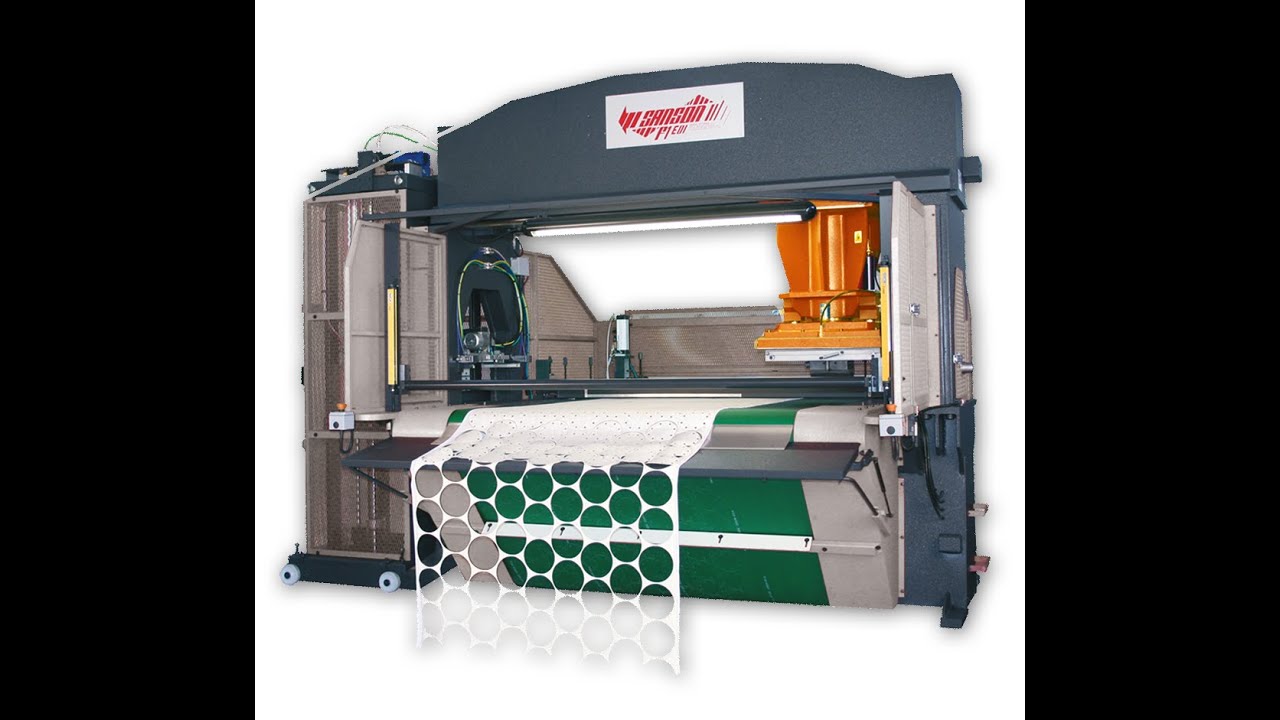
Chiesa are considered the market leader for industrial die cutting applications – particularly for the abrasive, gasket & automotive sectors. The long experience gained in the automatic cutting industry through thousands of installations and the steady dialog with our customers helped in creating a reliable, safe, user friendly performing product.
These die cutting systems are extremely efficient. The robust structure and the quality of mechanical components allow cutting speeds beyond 100 punches per minute, with a precision of a few hundredth of a millimeter, which allows parts to be kept as close as possible, increasing the material savings & cutting belt life.
The cutting power, up to 110 tons, is kept steady even for extremely long production runs allowing these machines to cut hard materials of high thickness, in single or multiple layers, and use multiple dies or dies with long blade development.
Automatic knockout, stacing & Rewinding System
Unloading converyor belt
For finished geometries up to 350mm in maximum diameter, placed on the side of the machine.
Up & down movement of conveyor
To match disc quantities stacked, programmable progress-indexing, and programmable disc quantities.
Discharge device (expulsion unit) with adjustable stroke
The upper and lower steel plates will be 8mm thich, with one set designed for 9" diameter discs.
Ejection device
Designed for (TBD Geometry - 2 Sets included), with optimized software according to the pre-determined width of the material.
Complete knockout device
mounted on movable casters for easy removal from the workstation when the operator wants to work in "standard" mode.
Single outboard rewind device with precise tension control
To recover the material scrap. The rewind will need to be aligned and mounted to the floor with adequate space povided for the module knockout and stacking unit.
Introduced at 2024 Open House
Automatic Robotic unloading System
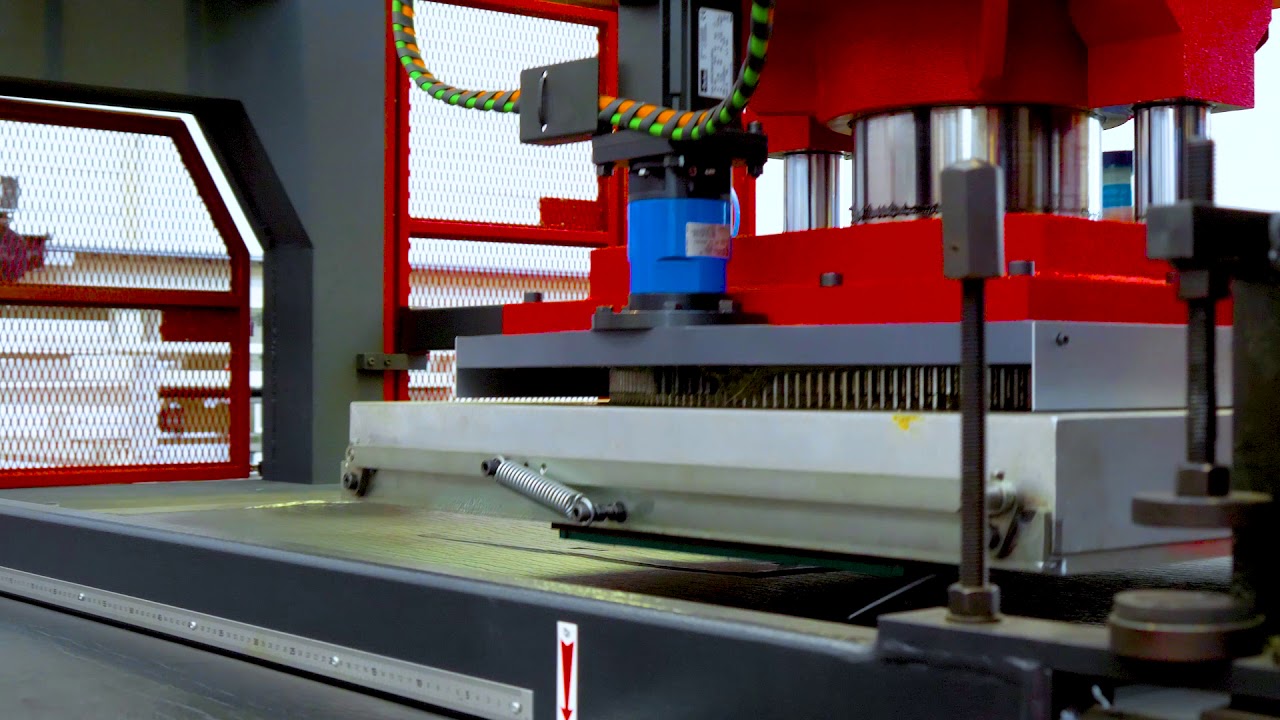
Stroke / Maximum reach | 850mm |
Maximum payload capacity | 12kgs / Rated at 3kgs |
Operating Range | J1 340° / J2 290° / J3 (z) 350mm / J4 (0 axis) 720° |
Maximum composite speed | 11,350 mm/s |
Cycle time (25 x 300 x 25mm w/ 2kg load) | 0.30 second |
Position repeatability | X/Y Direction +/-0.015mm / J3 (z) +/-0.010mm |
Drive system | AC Servo |
Position detection method | Absolute encoder |
Two (2) / ea. High performance Mitsubishi SCARA Robots (4-axis)
Two (2) / ea. Vacuum Gripping/Picking devices with suction cups
As noted, two gripping devices are included but, the “picking devices” could supplied with suction cups as shown. Matrix suction grippers (300mm x 400mm) or “needle style” pickers, for open cell foam materials. (Final TBD)
Two (2) / ea. Laser scanner safety devices
For the robots and one(1) laser scanner for front protection. The laser ray covers the area around the robot arm movement (complete rotational axis) and the dimensions of the areas (zones) of intervention can be defined accordingly.
One (1) Out-feed conveyor table
Approximately 1800mm (W) x 5245mm (L), complete with clamping beams to hold matrix securely in place.
Two (2) side conveyor belts
One is aproximately 1000mm (W) x 3500mm (L) and the second 1000mm (W) x 6000mm (L), for the unloading, stacking and transport of the die cut pieces.
Material Handling Solutions
International Unwinders-Rewinders
PDF - 720 KB
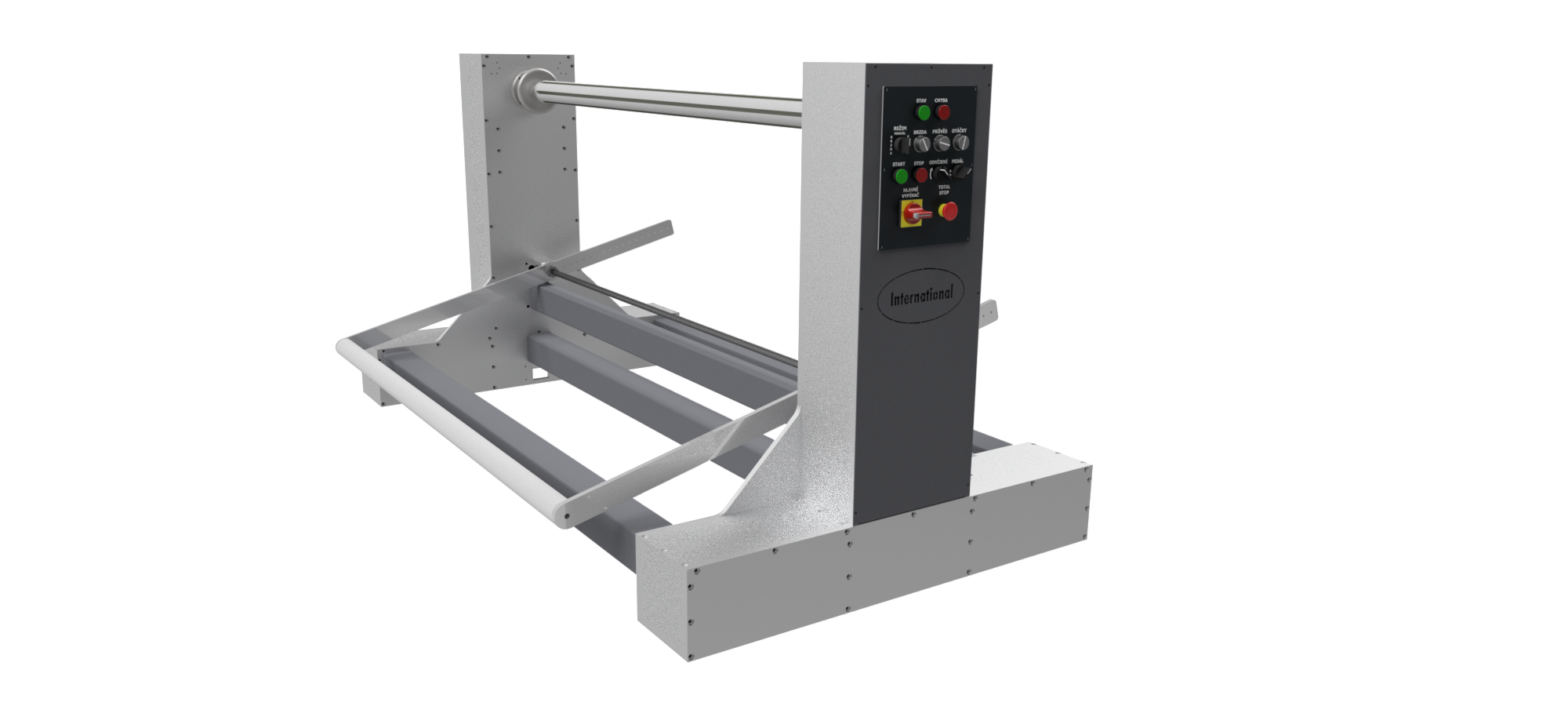
The machine is equipped with:
Dancer: A sensor for monitoring material sag, controlling the drive shaft based on its data. Winding with sag allows for reduced stretching during material uptake
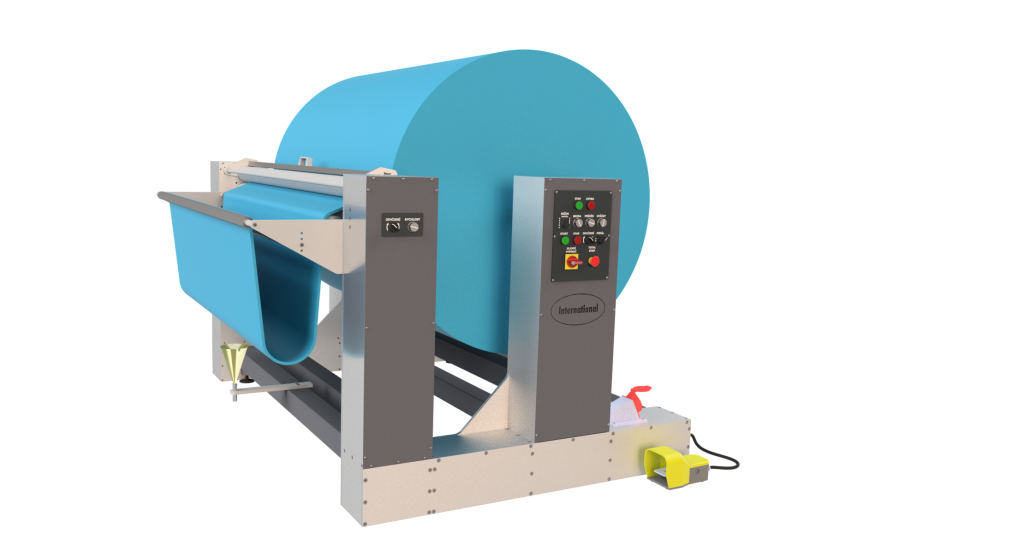
The machine is equipped with:
Puller: Assists the drive during winding and creates tension between subsequent machines and the unwinder.
Sensor: Monitors material sag, adjusting winding speed accordingly
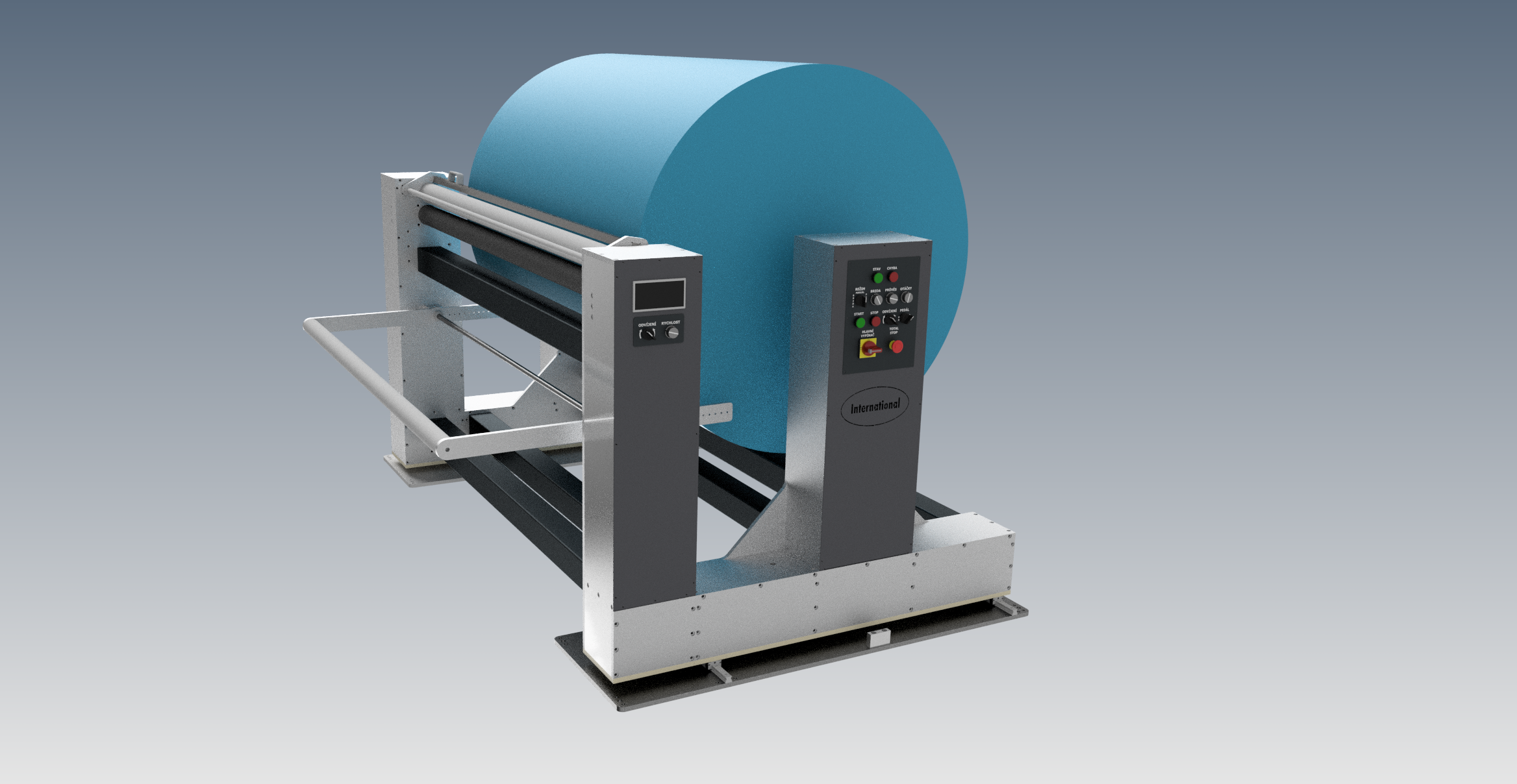
The machine is equipped with:
Dancer: A sensor for monitoring material sag, facilitating reduced stretching during material uptake.
Puller: Assists the drive during winding and creates tension between subsequent machines and the unwinder.
Side Control: A device for aligning winding; it adjusts the position lightly if the material is unwound off-center.
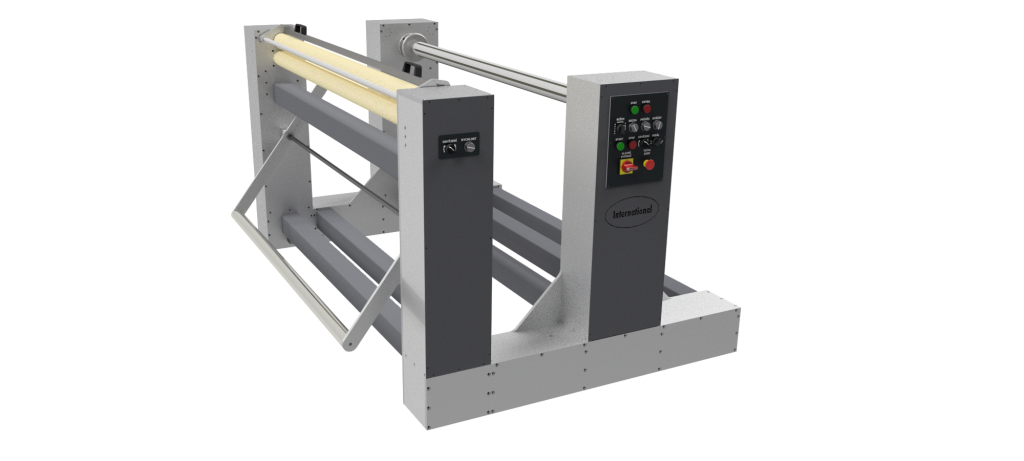
The machine is equipped with:
Dancer: A sensor for monitoring material sag, optimizing drive shaft control for reduced stretching during material uptake.
Puller: Assists the drive during winding and creates tension between subsequent machines and the unwinder
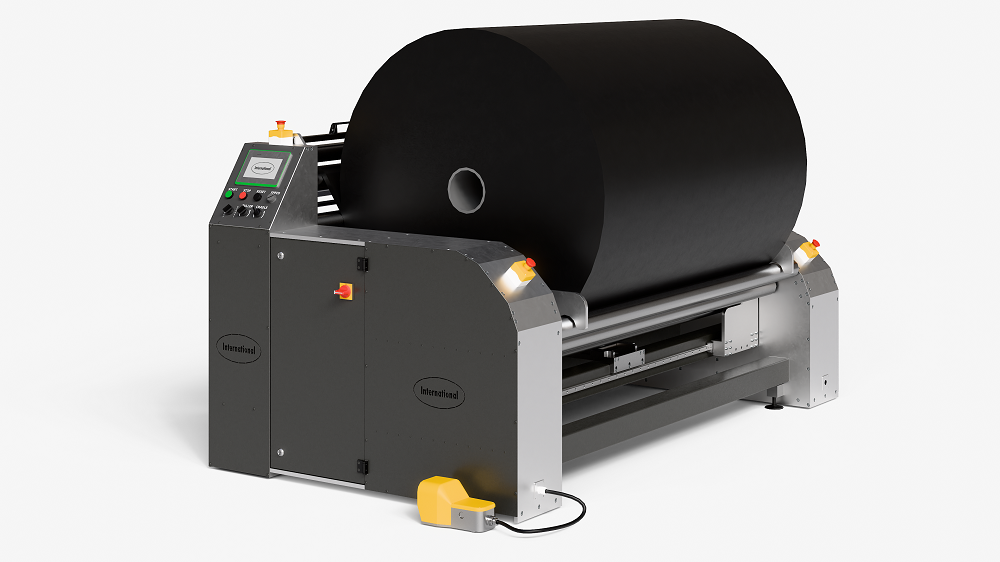
The machine is equipped with:
Dancer: For sag monitoring and optimized drive puller, ensuring reduced material stretching during uptake.
Puller: Assists the drive during winding.
Side Control: Ensures precise winding alignment, adjusting position if material is unwound off-center.
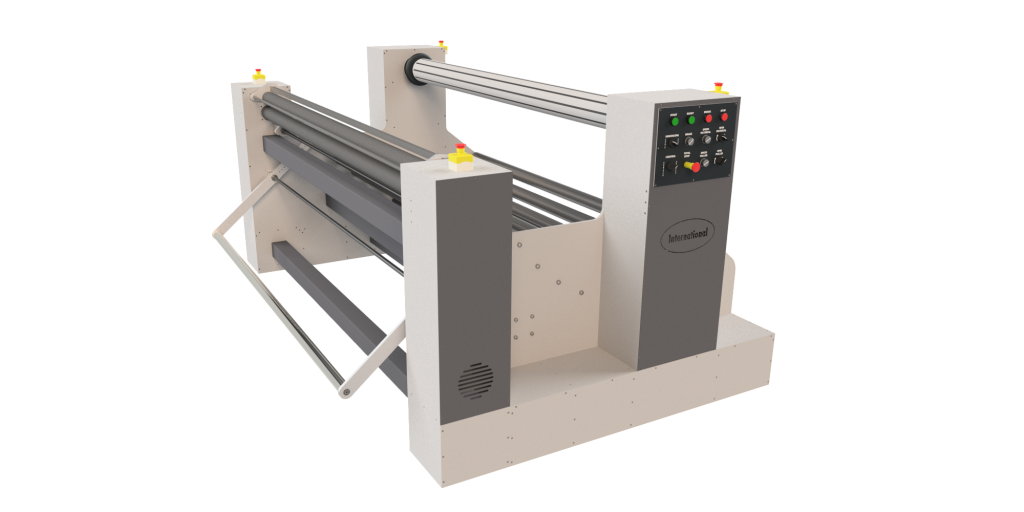
The machine is equipped with:
Dancer: For sag monitoring and optimized drive shaft control, minimizing material stretching during uptake.
Puller: Assists the drive during winding.
Side Control: For accurate winding alignment, making slight adjustments if material is unwound off-center
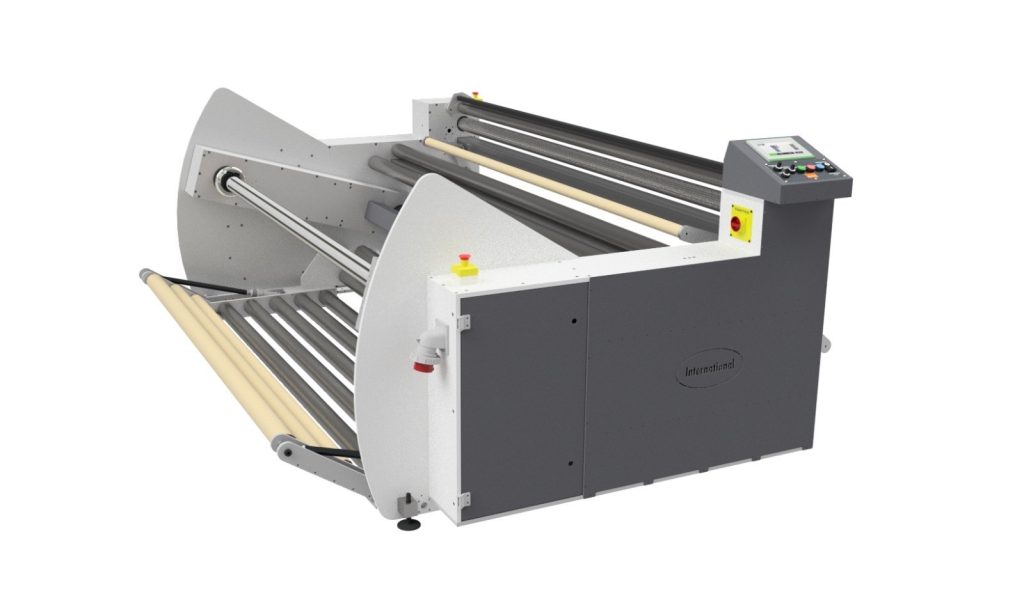
The machine is equipped with:
Loader: A device for enhanced material handling, automatically raised by the machine for improved efficiency.
Puller: Assists the drive during winding
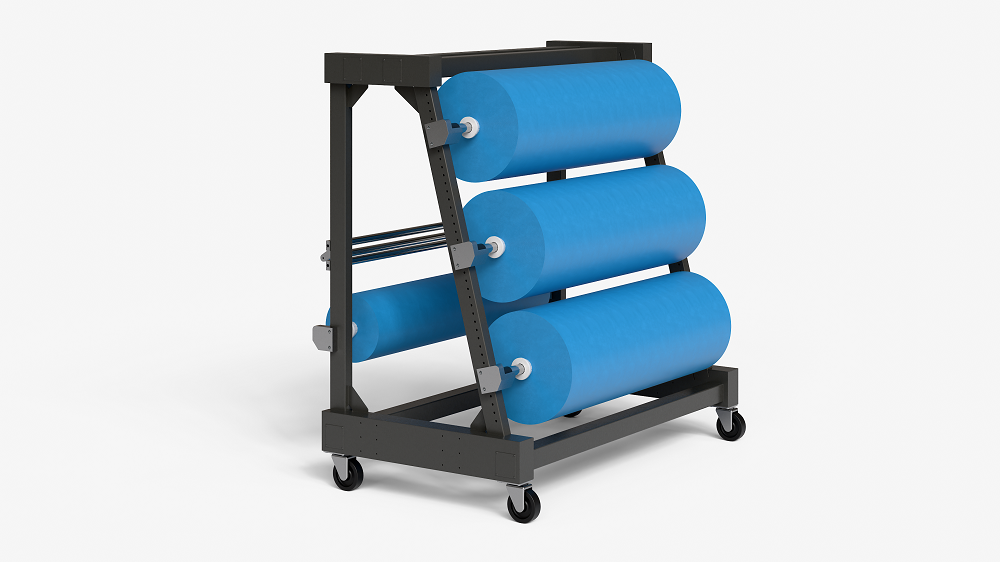
The machine is equipped with:
Holder: A device for shaft retention, with a maximum capacity of 4 units.
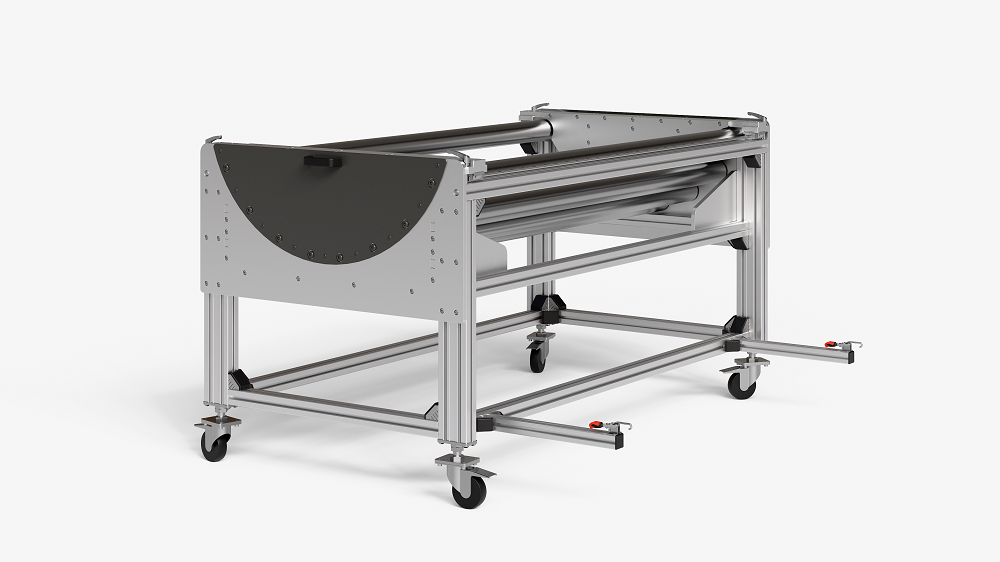
Downloads
Download F1 with Robots Layout
PDF - 500 KB
Advanced
Nestting Software
These powerful automatic nesting systems have been specifically designed by Chiesa on the basis of the experience gained with hundreds of die cutting machines installed at customers from all industries exclusively by Manufacturers Supplies.
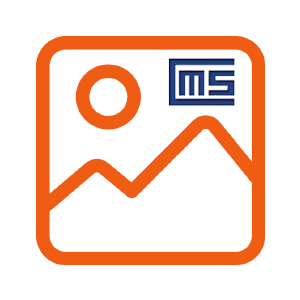
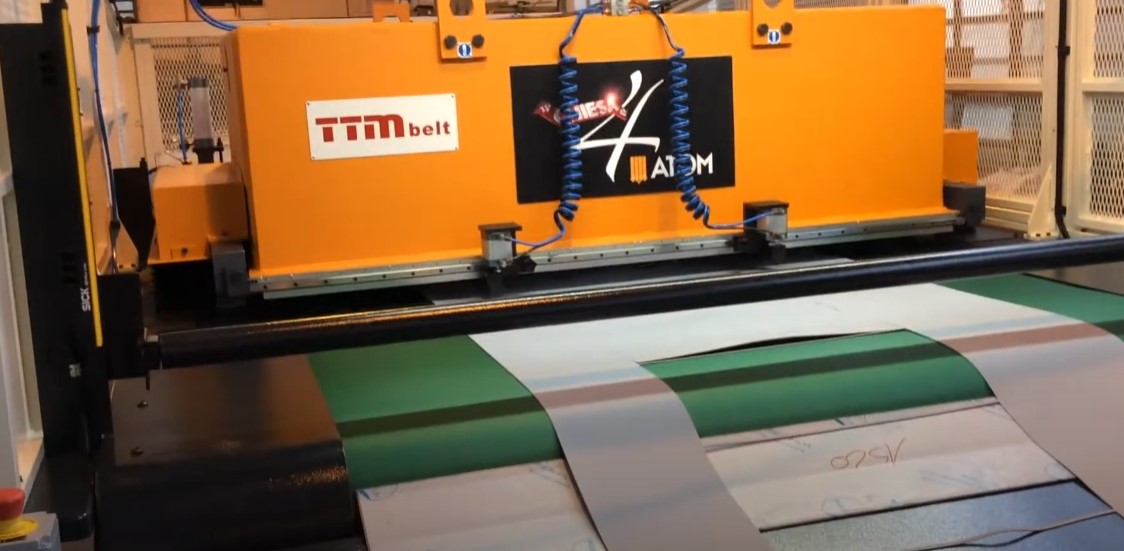
Once the best material optimization is obtained, the graphic image of the result is displayed on the systems touchscreen monitor along with the data relating to the cost of an individual piece or the entire run, the production time, the yield etc.. The cutting programs can be transferred to the press either manually (by drive) or automatically via serial connection.
Unrivalled
Algorithms
The nesting software gives the best material utilization and the fastest cutting speeds available on today’s market. Ultimate job flexibility is achieved without the need to change your current production methods. All nesting features are completely automatic. You can nest any shape-regular or irregular, into sheets or rolls and sheets joined into rolls. You can nest a breakdown of different shapes, sizes and quantities in a single run-optimizing material utilization. Bias or diagonal cutting is a standard feature. Precise job costing and timings may be calculated instantly. In this way your material ordering and stock level can be tightly controlled and kept down to a minimum.
Die
Digitization
It is possible to digitize quickly and easily the dies in order to have them ready for automatic nesting. The digitization solves any problem of die centering and positioning on the support plate. When nesting irregular shapes, a special die digitizer is used to transfer the cutting tool pattern into the computer memory in a few seconds with an accuracy of 0.1mm. The profiles of the cutting tools are memorized in the system and no further adjustments are required when nesting or cutting. Special constraints of directionality, coupling or cutting sequences can be specified by the operator. Just select with a mouse the tools and materials and then type the number of pieces you need to cut. The automatic nesting will automatically choose the best nest for your job in a matter of seconds. The work schedule is transferred to the machine and run with no further manual intervention. The operator just needs to start the program following the instructions on the screen.
ATOM Flashnest
Advanced Nesting Software
For over 25 years, ATOM manufactured a complete range of CNC die cutting presses and systems with advanced, powerful nesting software packages tailored for specific markets & applications. When ATOM & CHIESA joined forces in 2012 to offer an even wider range of CNC traveling head presses, they teamed their software personnel to create a conversion software, INTELLI-CONVERTER, which will allow existing ATOM customer’s the ability to use their current layouts & shape files on their new CHIESA CNC Die Cutting Press and will also allow them to continue using the nesting software that they have grown accustomed to over the years.