FEBA
Duplex Slitters-Rewinders
FEBA Duplex Slitters-Rewinders are available with cantilevered or lift-out rewind shafts and are the most advanced and versatile duplex slitting & rewinding system for converting larger diameter finished rolls of self-adhesive & non-adhesive materials, films with our without adhesives, foil, foam tapes, laminated foams, vinyl, PET, styrene, paper, laminates and similar materials up to a maximum diameter of 800mm.
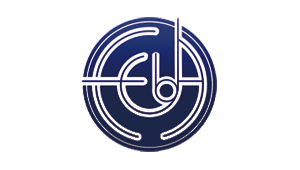
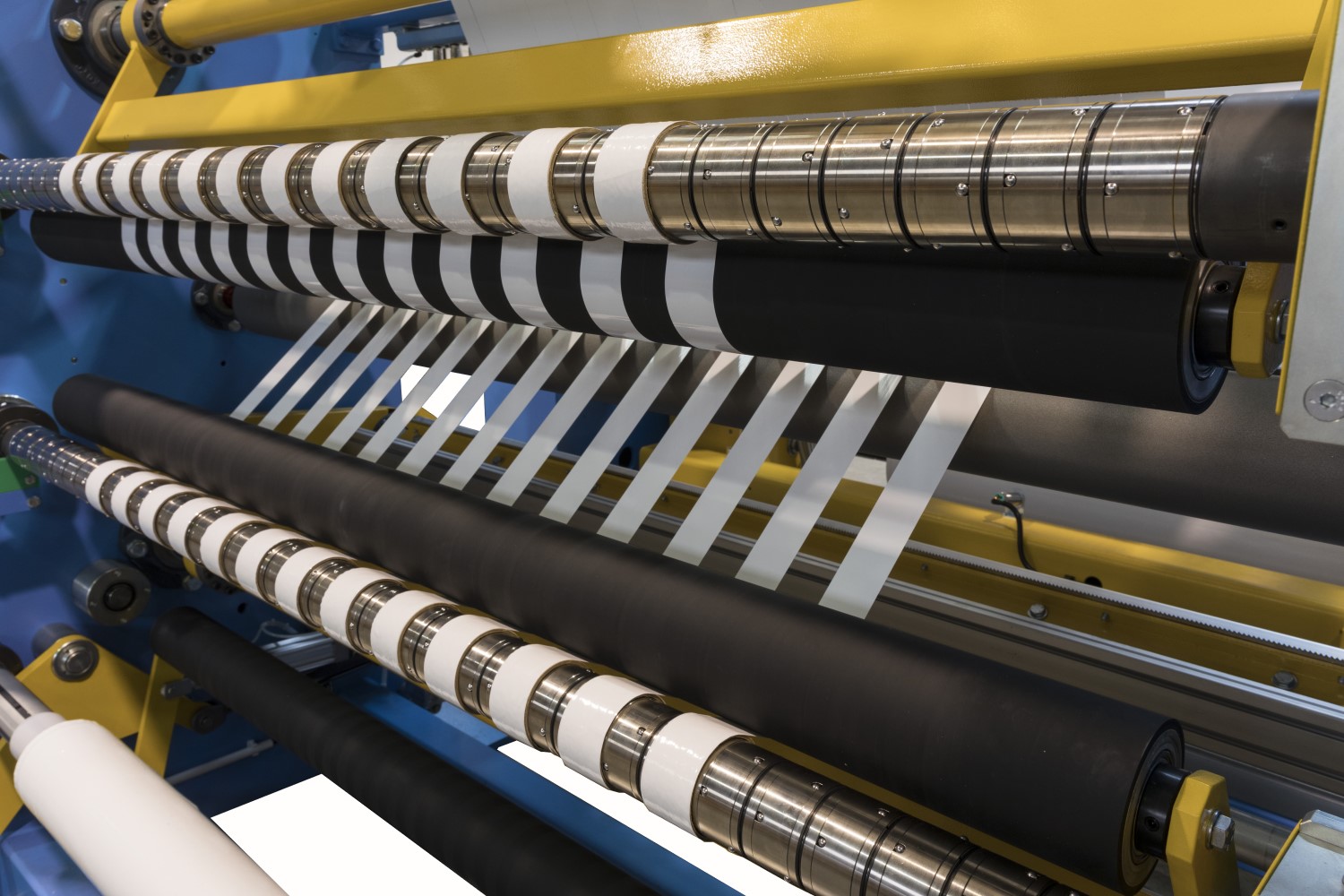
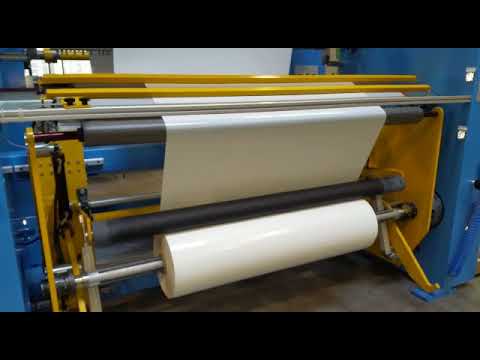
FEBA Duplex Slitters-Rewinders are available with cantilevered or lift-out rewind shafts and are the most advanced and versatile duplex slitting & rewinding system for converting larger diameter finished rolls of self-adhesive & non-adhesive materials, films with our without adhesives, foil, foam tapes, laminated foams, vinyl, PET, styrene, paper, laminates and similar materials up to a maximum diameter of 800mm. FEBA’s differential air shafts & servo driven lay-on-roller systems, provide the ability to slit and rewind the most difficult light gauge films & complex laminate materials. The FEBA Duplex Slitter-Rewinder can be configured with multiple types of slitting systems including razor blade, shear-scissor cut and score cut to accommodate diverse applications. For increased versatility, an additional lower expansion shaft can be added and utilized as a log winder for logging-rewinding rolls up to 600mm in diameter with an adjustable pressure lay-on-roller for perfect rewound tension.
Slitters-Rewinders
Duplex Slitters-Rewinders
FEBA develops advanced, proven technologies that increase production, simplify operations, significantly reduce downtime, and provide outstanding finished roll quality with solutions customized to meet your exact converting requirements. Innovative systems for unwind tension and rewind torque control allows for minimal waste, and rolls of perfect quality for every type of material, with the production process controlled by a recipe driven system. FEBA Duplex slitting & rewinding machines can also include lamination & delamination stations, liner recovery rewinds, in-line perforating units, splicing tables, web inspection & web-break detection systems, in-line labeling, lower log winders, mechanical or vacuum trim recovery, automatic roll unloading via robotics, shaft transfer systems w/ automatic core loading, and in-line or off-line packaging solutions.
FEBA Duplex Slitter-Rewinder Features
Unwind Technology
Slitting Modules – Razor, Scissor or Score
Razor blade slitting is most common used slitting method for a wide variety of materials since the razor blades are inexpensive and simple to setup and replace. Razor slitting can be done ‘in air’ or in a ‘grooved roller’ to support the web during slitting.
Scissor cut, or shear, is the most versatile slitting method as it covers the broadest range of materials. Scissor cut (shear cut) slitting can be used for a wide variety of papers, films, laminates and foils. Shear slitting variations can be ‘tangential/kiss’ or ‘wrap’ shear which involves a loaded male blade against a female ring, creating a scissoring effect to slit the web. Shear slitting typically provides the highest quality edge quality. Interchangeable groups for dedicated widths and “universal” groups for different widths.
Score or ‘crush cutting’ is commonly used for self-adhesives and some paper based materials. The score knife is a pneumatically loaded with a circular blade against a hardened steel anvil roller. The knife then “crushes” the web against the anvil. Generally, slit edges are not of the highest quality, but score slitting is quick and very easy to set-up and adjust the slitting widths.
Web Pass & Lay On Roll Technology
The FEBA Duplex Slitter-Rewinder is equipped with smoothed path rollers made of steel, PLASMA & Silicone RUBBER coated where needed, and are positioned in close proximity for ideal handling of self-wound and linear adhesive materials.The web pass rollers are made of chromed aluminum and steel are of different diameters in order to grant progressive thread up. A fixed or variable curvature “banana or bowed” made of anti-static rubber is installed to prevent wrinkles in the material allowing the slitter-rewinder to run at optimal speeds.
FEBA’s lay-on roller technology operates in two different modes: 1) Pressure & 2) Minimum Gap. The first mode features a more sensitive pneumatic or servo driven system to provide constant nip pressure on the slit rolls. By raising the entire lay-on roll system with an actuator (pneumatically or via servo), the weight does not factor into the pressure applied to the rewinding rolls. The 2nd mode, minimum gap, utilizes a servo driven actuator to maintain a constant fixed gap between the lay-on roll and rewound roll which is the most common winding method used for self-adhesive tapes and protection films. The rewinding tension adjustment is separate from the main drive and is fully adjustable through AC motors.
Differential-Friction Rewind Shafts
Differential air shafts or friction shafts are ideal for tension sensitive materials, and provides excellent stability for narrow rolls. Various width frictions (determined by finished slit width) are stacked across the entire shaft eliminating the need to setup spacers. When rewinding is complete, the roll locks automatically disengage for the finished rolls to be unloaded. Differential rewinding is obtained by strictly controlling the air pressure distributed internally across the roll locks. Tension is programmed into the touch screen and is proportional to the length of the rewinding cores. Because of this, converters have the flexibility to rewind rolls of different widths across the same shaft.
Lower Log Winder – Increased Versatility
For increased versatility, the FEBA Duplex Slitter Rewinder can be equipped with a lower shaft for log winding various self-adhesive materials. A rewind lay-on roller with adjustable pressure is installed for perfect log wind quality and a jumbo roll lifting device is available for easy loading of the finished logs, up to a maximum diameter of 600mm.