FEBA
Laminators & Laminating Systems
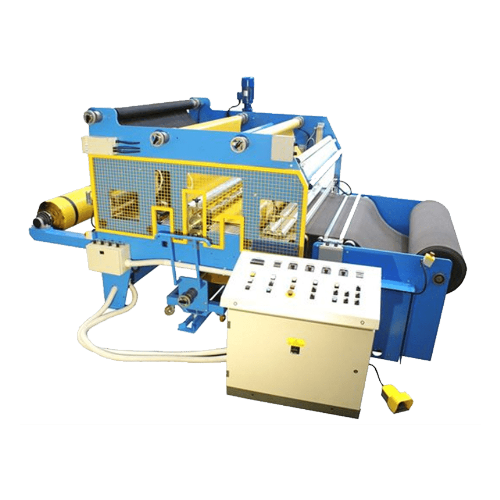
- Description
- Technical Specifications
FEBA Srl Converting Machinery engineers and manufactures a wide range of standard laminators & custom laminating systems for a variety of industries. FEBA specializes in technologies for the lamination of all foam materials like PE polyethylene, PP polypropylene, EVA, open cell, closed cell, cross-link foam as well adhesive & non-adhesive tapes and textile materials. The FEBA Systems Laminator can be configured with single or multi-layer lamination, liner removal, scissor cut, pressure cut and powered rotary slitting, embossing, corona treating, sheeting both semi-automatic & fully automatic (flying knife) and rewinding in wide web or narrow widths.
FEBA offers a wide range of material handling solutions and options including center & surface unwinds, automatic web guide systems, various tensioning control devices including belt-style lay-on-rollers, sheet handling both manual and automatic, center & surface winders, & accumulators. For heat activated adhesives, the FEBA Laminator can be equipped with infrared preheaters, infrared heated calendars or hot oil cylinders with independent control of each calendar station.
The FEBA Laminating Systems are designed accordingly to meet the customer’s specific converting application and material specifications.
FEBA Laminating Technologies
Main Unwind Unit (Jumbo Log)
Special belt style “lay-on-roller” with photoelectric barrier. The unit is driven up/down via pneumatic pistons with adjustable pressure, while it is powered (rotation) via Brushless motor with feedback to the PLC with the ability to adjust the speed to feed the material without tension.
Belt Style Lamination Calendar
The belt style lamination calendar is composed of two large diameter rolls linked with an anti-adhesive belt; this unit is fitted onto four electro-actuator units powered with a brushless motor. The four adjustments (One on each corner) are independent via four brushless motors to enable the lamination of the foam onto the single sided tape with soft increasing pressure. This is to ensure that the material is certainly in touch with the adhesive tape without creating any tension and all working parameters are stored via recipe.
Self-Adhesive (PSA) Unwinds
The upper and lower unwinds are to keep the single sided tape or adhesive film/net to be transferred. The brake power is controlled by a pneumatic proportional valve + SONAR so that while the diameter is decreasing, the brake tension will also decrease automatically. The pneumatic power in % (0-100%) is stored into the recipe.
Hot Oil Heating Unit
The most accurate and reliable heating source for heated activated lamination processes is hot oil. The FEBA Systems Laminators are with a hot oil unit which regulates the temperature from 0-150°Celsius and controls each hot oil cylinder installed on the machine independently. Each cylinder is equipped with an infrared sensor for the temperature feedback to the PLC (adjustments based on working environment temperature change) and the set operating temperature for each cylinder is stored in the recipe.
Longitudinal Powered Slitting Unit
A variety of slitting systems can be installed on the FEBA Laminator, including razor blade, scissor cut (blade & counter blade) and pressure cut (air score) units. For thicker-denser materials, a powered slitting unit is installed consisting of (X) rotating blades and blade holders for a minimum slitting width of 200mm. The powered blade holders are installed on linear bearing assemblies, and the position is locked manually via brake directly onto the bearings. Each blade is lubricated with a felt wiper and the lubrication is supplied via a hydraulic proportional pump system. In addition, for materials requiring an extremely sharp blade, a double sided diamond wheel sharpening device is installed with auto frequency controlled via the HMI.
Automatic Sheeting Unit (Flying Knife)
For roll to sheet applications, the FEBA Systems Laminator can be equipped with an automatic “flying knife” sheeting unit. This unit is equipped with three 0,5 HP motors : two for the Y travel movement of the pneumatic grippers for material indexing, and one for the X travel to traverse the blade across the material. The powered rotary blade to “sheet” the material is driven a 0,75HP AC motor with variable rotational speeds from 10-500 RPM. The blade is lubricated with a felt wiper and the lubrication is supplied via a hydraulic proportional pump system. In addition, for materials requiring an extremely sharp blade, a double sided diamond wheel sharpening device is installed with auto frequency controlled via the HMI.
Main Rewind Unit
The main outboard rewind unit is equipped with a 4 HP AC Motor + encoder for the proportional rewinding and perfect tension control. SONAR provides feedback to the digital drive to keep the tension constant with a maximum of 35 Kg (material dependent).
HMI – Recipe Driven System
To store all the working parameters of the machine, the FEBA Laminator is equipped with an OMRON Touchscreen HMI and controls all the unwind tensions (proportional brakes), belt lamination unit height settings (4 corners), calendar height adjustment (material thickness), individual temperature control (hot oil cylinders), operating speeds, sheet counter and roll length as running, slitting blades speeds in RPM, auto sharpening frequency, and rewind tension control. In addition, an Ethernet Connection is provided for remote diagnostic assistance.
Fabric to Foam Lamination (Multi-Layer Lamination)
Adhesive-based fabric-to-foam lamination reduces cost and improves product quality in the manufacture of upholstery, automotive interiors, acoustical wallboards, carpet, shoes and office furniture.
- Meet environmental regulations by eliminating flame lamination.
- Increase overall line speeds and throughput.
- Precisely control the exact volume of adhesive applied.
- Use non-foam materials such as breathable films and nonwovens.