Guidolin Girotto
RO 350
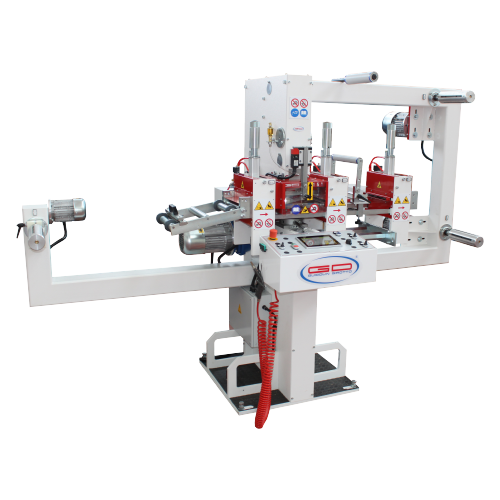
- Description
- Technical Specifications
- Modular Stations
- Points of Strenghts
The Guidolin Girotto rotary converting system, model RO 350, has been designed and developed for the die cutting & kiss cutting of adhesive and double sided adhesive tapes, foam tapes and any other technical flexible material to satisfy the requirements of high production with extreme cutting precision. Its optimal field of application is represented by the following industries: automotive, aerospace, adhesive & double sided adhesive tapes, composites, electronics, medical products, felts & textiles, gaskets, packaging & plastics.
The RO 350 rotary converting press has a useful working width of 350mm and is available in three body lengths; 1.7M, 2.2M and 3.05M with production output speeds ranging from 0-100 meters per minute. The Guidolin rotary die cutting machine is equipped with a single brushless servo motor and coupled with an in-line drive shaft and precision worm gears in order to grant the same torque strength from zero to maximum working speed. In addition, unique to the Guidolin product, the machine can operate in both start/stop mode & continuous mode; in start/stop mode, the rotation of the tool, pneumatic expulsion unit or transversal guillotine occurs according to the desired quote set in the Touch-screen controller.
The die cutting stations, with either micro-metrical or servo registration, can accommodate both magnetic flexible tooling and hardened rotary tooling and can also be designed to accept the customer’s existing tooling (gear pitch ratio). The solid frame construction, modular stations with various optional systems, & computer controlled system make the RO 350 rotary cutting machine versatile, fast & easy to operate; guaranteeing a quick transition from job-to-job which minimizes machine downtime, reduces labor and overall operating expenses. Being modular, with every station moveable, one machine can be configured to process a wide variety of materials making it the ideal solution for numerous applications. Furthermore, all the nip roll conveyors and lamination modules come standard with a single hand wheel screw to set the rolls perfectly parallel with the material eliminating the “walking” of the web commonly seen with twin adjustable transports. The standard 7” color touchscreen stores up to 500 different recipes and can track the production output by pieces or material length.
Our team of engineers reviews your application and requirements, listen to your needs, and respond to offer a more innovative die cutting & converting solution to improve your current manufacturing process. Each machine is designed after a careful evaluation of the customer needs, the challenges of the material to be converted, therefore every machine produced is “made to order” for each client.
Contact us to get Technical Specifications
The modular stations and available optional systems are listed below and can be arranged accordingly based on the application, now or at any point in the future.
- Main Unwind with electronic brake controlled by an ultrasonic sensor
- Automatic web tension control
- Automatic web guide system with electronic control
- One, two or three friction unwinds with lamination on the axes
- Lamination group with silicone covered feed rolls & single – centered – adjustable hand wheel
- Lower friction unwinds
- Lower motorized rewinds
- Motorized rewind with adjustable bar to remove the scrap
- Die cutting station with transversal micrometric regulation
- Die cutting station with longitudinal micrometric regulation
- Die cutting station with servo registration
- Reverse Die cutting station to cut from below
- Pneumatic expulsion /knock-out system (start/stop mode)
- Razor blade slitting unit
- Scissor cut slitting unit (Bladed & Counter-blade)
- Rotary pressure cut slitting unit
- Transversal guillotine cutting system (to create predetermined sets)
- Automatic stacking system
- Trolley to store stations while not in use
Modular Strengths
- Every station is movable
- Gears are worm gears for extra precision
- Fixed locating pins allow for quick change station to station
- Machine may be purchased with limited options to fill current needs and stations can be added as needed in the future
- Off-line trolley to stock the modular stations while not in use.
Simplicity Strengths
- Simple spring clutches, less electronics, less dials for operator adjustment & error
- Single brushless servo motor coupled with an in-line drive shaft and precision worm gears in order to grant the same torque strength from zero to maximum working speed
- Transport and Laminating stations have a single adjustment screw in the center, for easy closure allowing the path rollers to stay completely level – eliminating the wandering of the web – a common problem with dual adjustable transport rollers
Electronics & Software
- Touch screen with the ability to save parameters for 500 jobs
- Operate in both start/stop mode & continuous mode
- Can count in distance or parts cut based upon number of teeth and cavities in the die for precise count of either parts or distance traveled
- Although the desired speed can be saved for a job, the machine will not start until the speed control is set to zero to prevent crashing the web or injuring an operator.
- Sonar to control the tension of the lower unwinds for sensitive materials when needed, controlled in touch screen PLC.
- Automatic web guide system for the automatic alignment of the material with electronic edge guide to grant a constant & suitable alignment of the material with seperate electronic control device for set-up