Chiesa
F1 EDI CNC TRAVELING HEAD PRESS
The Chiesa F1 EDI CNC Traveling Head Press, with 3 numerically controlled axes, incorporates an electrically servo driven cutting head without the use of hydraulics.
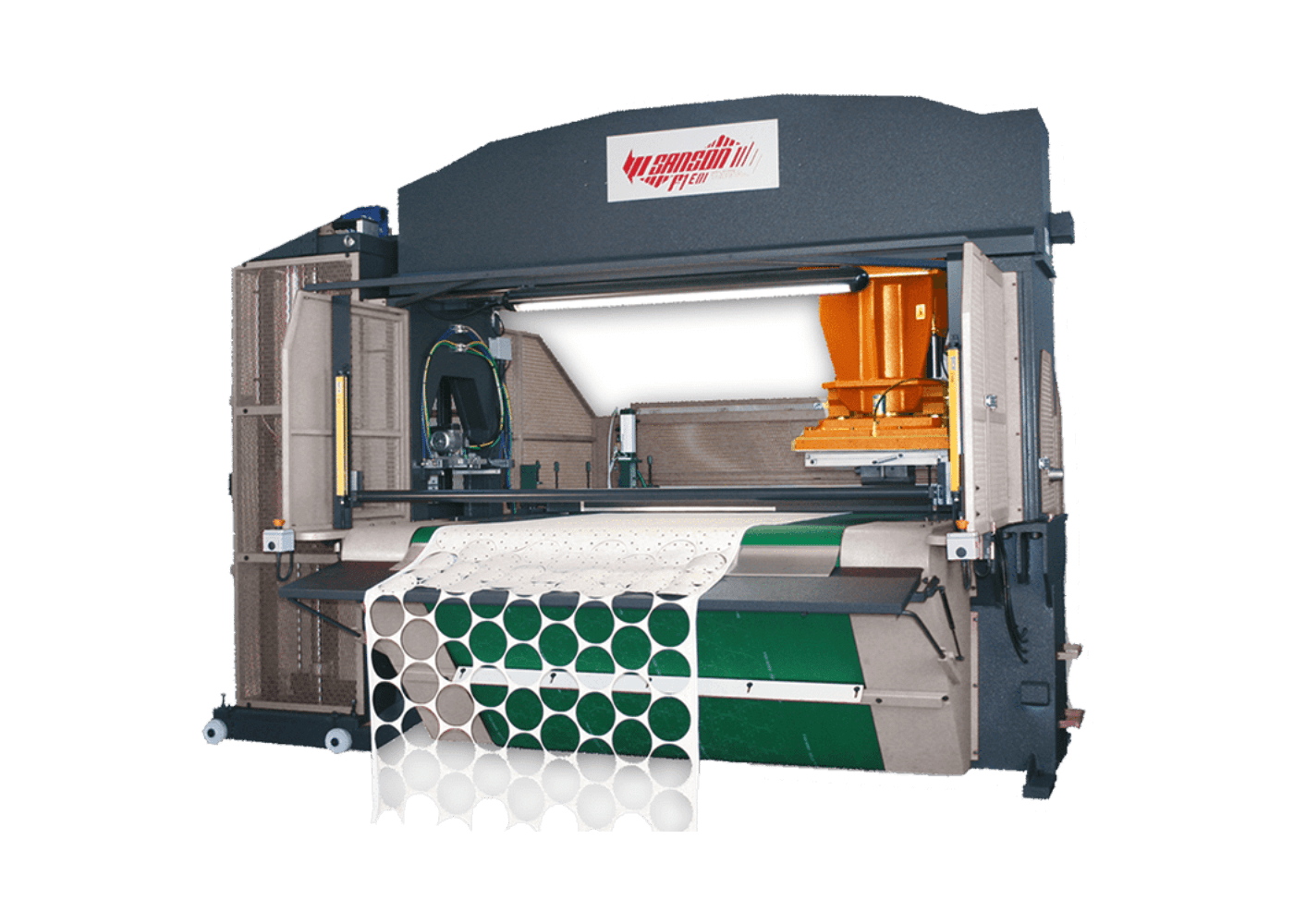
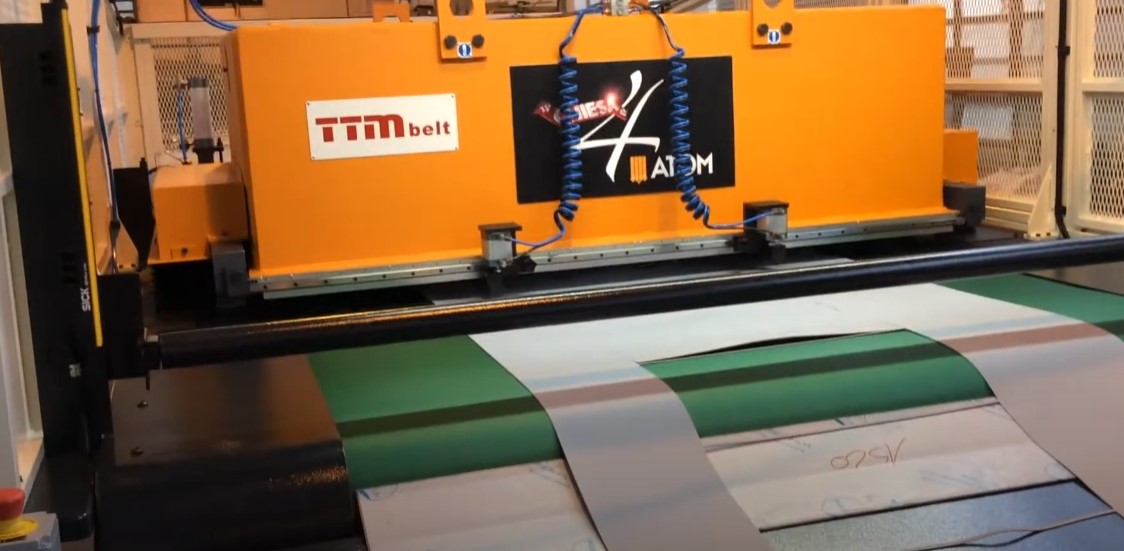
Chiesa are considered the market leader for industrial die cutting applications – particularly for the abrasive, gasket & automotive sectors. The long experience gained in the automatic cutting industry through thousands of installations and the steady dialog with our customers helped in creating a reliable, safe, user friendly performing product.
These die cutting systems are extremely efficient. The robust structure and the quality of mechanical components allow cutting speeds beyond 100 punches per minute, with a precision of a few hundredth of a millimeter, which allows parts to be kept as close as possible, increasing the material savings & cutting belt life.
Modular Feeding Systems
- Cutting Belt & Feeding Clamps: Suitable to cut any type of synthetic material both in rolls and sheets, loaded both from the front or back of die cutting press; the material is moved and fixed by three independent clamps. One clamp is mobile and supports the belt in the movement of the material to grant the maximum positioning of the material(s) even for soft, elastic products, cut in single or multiple ply.
- Mobile Cutting Pad & Clamps: Suitable to cut sheeted goods only, both in single & multiple layers. The sheets are loaded onto a polypropylene cutting pad with automatic movement and equipped with special clamps. The clamps allow the cutting of multiple layers without stapling.
-
Automatic Sheet Feeding: The material is loaded onto a hydraulic platform, both in single or stapled multiple layers. A special vacuum suction cup device grips the material and positions it onto the back of the machine. The feeding system will automatically stop the machine when there is no longer material available. The sheet feed system is available on all models equipped with the cutting belt & clamps. The system can also be equipped with an automatic part unloading device.
The advanced nesting software allows to calculate, with considerable precision, for each material consumption and time required (thus labor cost) in order to make accurate simulations of the cutting cost, enabling better production planning and more precise offers to customers.
Points of Strength
- EDI Technology: The first electrically servo driven automatic CNC die cutting press (NO HYDRAULICS) – Eliminates all components associated with hydraulics; i.e. hydraulic oil, seals, pumps, valves, hoses, filters, hydraulic tank etc..
- “Pit-Stop” Automatic Die Changing Device: Originally developed for the gasket industry to utilize the use of cuts without using a multi-cavity tool which imposes the cutting of an equal number of the main shape & filler component. This device also gained interest in the abrasive industry which allowed the pre-programming of cycles prior to tool wear and reducing any down time or loss of material. It is also possible to schedule the daily production orders through dedicated “Job Manager” software.
- Energy Savings – GREEN Technology: Reduction of direct power consumption by 50% – the higher power is only required while cutting; minimal power is absorbed while in “hold” or during the accessory operation like Y & Z axes movements.
- Rapid Die Set-Up: Compared to a traditional hydraulic system, no down-stroke movement in low pressure is required to the set the die height. Simply enter the tool height, 23.8mm as an example, and the die setting is complete.
- Accurate Die Setting: The die setting tolerance is in the range of one hundredth of a millimeter (0.01mm), thus allowing a perfect penetration of the die into the material & remarkably reducing the belt consumption. The setting is so accurate; you are able to perform kiss-cutting operations on laminated materials.
- Reduced Noise Emissions: The electrically servo driven cutting head is virtually noiseless; you can barely hear the machine operate.
- Reduced Maintenance: The ball screw driving the cutting head does not require any maintenance. The absence of the hydraulic system avoids the need of maintenance, like hydraulic oil & filter replacement, gasket & seal wear, high-pressure hoses, pumps, valves etc.
- Air Conditioned Electrical Cabinet: Keeps the electronics cool and eliminates any dust or debris from entering the cabinet.
Advantages
- Rigid Construction – Designed for Reliability & Low Maintenance: This die cutting press is a pure CNC machine, not a manual press retrofitted with automatic features. The construction of the press, designed on the latest CAD systems, is the most robust and rigid available. The ball screw driving the cutting head does not require any maintenance. The absence of the hydraulic system avoids the need of maintenance, like oil & filter replacement, seal & gasket wear, high-pressure hydraulic hoses etc..
- Material Savings: The quality of design and components allows extreme precision in positioning, minimizing the distance between cut pieces. The automatic nesting software calculates automatically optimal layouts to take advantage of the allowed precision.
- Time Savings and Increased Flexibility: The software can prepare the cutting program in a few seconds. Using a die plate it is possible to change the die very quickly from the side of the press or when equipped with the automatic tool changing device, a die can be changed in as little as 10 seconds – automatically. This fast configuration change makes even the cutting of small production batches, of a few hundred parts, cost effective.
- Labor Savings: The system allows high quality cutting even with inexperienced operators. A single CNC cutting machine can substitute 3-5 traditional trolley presses and their skilled operators. The die setting is quite simple and can be done by simply entering in the tool height unlike a hydraulic system which requires a low pressure set-up.
- Low Operating Costs: The special design, which takes advantage of patented Chiesa solutions, grants high cutting power and speed with limited power consumption. The higher power is required when cutting only, very low power is absorbed while in “hold” or during the accessory operation like axes movement. On average, our customers typically see a 50% reduction in energy consumption when compared to traditional hydraulically operated die cutting presses. The quality of components reduces the maintenance costs and minimizes the time associated.
- Easy Operation: No special skills are required to operate the press. Your current press operators can use it. Machine programming and nesting may be carried out either locally or remotely from your production planning office. Cutting programs can be transferred through network or thumb drives. The work schedule automatically controls the press and informs the operators when material and tool changes are required. If your material width varies, or rush jobs require immediate priority, the operator can instantly re nest the schedule to accommodate these changes. Standard cutting tools are fitted onto a simple steel carrier plate and easily replaced on the cutting head in less than ten seconds via the automatic tool changing device.