FEBA
Turret Slitters-Rewinders
The innovative FEBA Turret-Style Slitter-Rewinders provide significant productivity gains when compared to traditional duplex style slitters and in some cases, can out-produce these style winders by 200-300%. The advanced technologies employed in the FEBA System precisely control roll quality and decrease down-time during finished roll change-out. Turret winders minimize down-time between cycles, offering the greatest advantage on high volume, long running, multi-set converting.
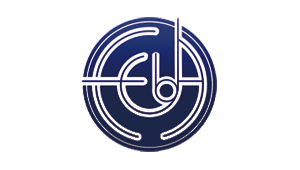

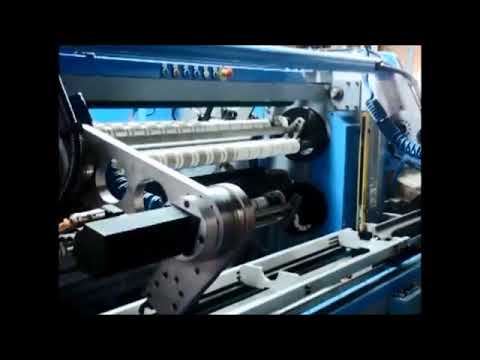
Slitters-Rewinders
Turret Slitters-Rewinders
Turret style slitters-rewinders are equipped with two rewinding stations, commonly referred to as “revolvers or turrets”, to automatically run in continuous fashion for maximum productivity & throughput. Two or three sets of rewind shafts minimize downtime by allowing the slitter to keep running while the finished rolls are unloaded and the new cores, pre-loaded on the shaft, are re-loaded into the machine automatically. Fully automatic cycles with auto tab application, final end cut and a variety of automated material handling solutions to further decrease the level of downtime for high volume converters. In-line rewind shaft transfer systems from the Slitter-Rewinder to the core hopper automate the roll removal and core loading process, and the robotic shaft manipulation system can be equipped to automate the shaft loading & unloading procedures for a fully automated solution. All of our Turret Slitter-Rewinders are engineered to work in-line with packaging machines and carton fillers, and can be equipped with various types of braked or driven unwinds. These automated cells can be customized to suit your unique specifications & production requirements.
FEBA Slitter-Rewinder Technology
Unwind Technology
Several unwind options have been engineered to integrate with FEBA’s various Duplex & Turret Style Slitters-Rewinders: 1) Braked, 2) Surface Driven & 3) Central Surface Double Drive. The standard integral unwind is available with an expandable shaft (3”, 6”, 10” or 12”) or as an option, shaft-less, designed to facilitate efficient handling of the master roll. The jumbo axe is motorized by an AC motor which will automatically decrease the break tension while the jumbo OD decreases in size with braking proportional to speed and roll diameter variations. Options for these unwind stands include a position regulated dancer, a “step” in-between unwind & slitter, liner recovery, servo driven perforating units, splice tables (pneumatic or v-groove), web break detection units, and automatic edge guide alignment systems.
Tension Control
Adjusting for the correct tension during the slitting operation is critical for tension sensitive materials. Closed-loop rewind tension control grants the operators the optimum level of control over the rewinding process. This option is particularly helpful for converters running tension-sensitive materials such as light gauge, extensible films.
Load cells are used to take tension readings for closed-loop rewind tension control. The slitter control system automatically adjusts the air pressure in the rewind shafts. This adjusts the rewind tension to match the load cell readings. This maintains the desired tension based on the base tension setting, taper tension setting and current roll diameter.
Slitting Modules – Razor, Scissor or Score
Razor blade slitting is most common used slitting method for a wide variety of materials since the razor blades are inexpensive and simple to setup and replace. Razor slitting can be done ‘in air’ or in a ‘grooved roller’ to support the web during slitting.
Scissor cut, or shear, is the most versatile slitting method as it covers the broadest range of materials. Scissor cut (shear cut) slitting can be used for a wide variety of papers, films, laminates and foils. Shear slitting variations can be ‘tangential/kiss’ or ‘wrap’ shear which involves a loaded male blade against a female ring, creating a scissoring effect to slit the web. Shear slitting typically provides the highest quality edge quality. Interchangeable groups for dedicated widths and “universal” groups for different widths.
Score or ‘crush cutting’ is commonly used for self-adhesives and some paper based materials. The score knife is a pneumatically loaded with a circular blade against a hardened steel anvil roller. The knife then “crushes” the web against the anvil. Generally, slit edges are not of the highest quality, but score slitting is quick and very easy to set-up and adjust the slitting widths.
Automatic Knife Positioning
Automatic knife positioning is an affordable upgrade option that virtually eliminates the blade set-up time and is especially effective with laser core positioning and differential friction shaft options. The blade positions are stored in each individual recipe and when recalled, the slitter-rewinder automatically configures the correct running parameters. Servos position the top and bottom knives, shear or score available, resulting in faster job changeovers, increased slitter run time, more rolls per shift with more consistent roll dimensions and quality.
Lay-On System Technology
FEBA’s lay-on roller technology operates in two different modes: 1) Pressure & 2) Minimum Gap. The first mode features a more sensitive pneumatic or servo driven system to provide constant nip pressure on the slit rolls. By raising the entire lay-on roll system with an actuator (pneumatically or via servo), the weight does not factor into the pressure applied to the rewinding rolls. The 2nd mode, minimum gap, utilizes a servo driven actuator to maintain a constant fixed gap between the lay-on roll and rewound roll which is the most common winding method used for self-adhesive tapes and protection films.
Differential-Friction Shafts
Rewind Shaft Transfer and Core Loading System
Robotic Shaft Manipulation System
To increase productivity, without costly downtime during the converting process, the FEBA Turret Slitters-Rewinders can be equipped with two robotic arms for the automatic shaft manipulation movement between the Slitter-Rewinder and Core Loader. Once the pre-programmed meterage length is reached, and the finished rolls are transversally cut to length and closed via tab-application, the turret completes the rotation for the next cycle to commence, and at that time the shafts with finished rolls are automatically unloaded via robotics. The shaft is placed into a trough, automatically removed from the finished rewound rolls via the shaft transfer system, and a driven conveyor moves the shaft to the core loader for the new cores to be loaded onto the friction shafts. During this process, the finished slit rolls are discharged horizontally or vertically to be transported by modular conveyor belts to the packaging line. The shaft with the pre-loaded cores is then transferred back from the core loader to the front of the machine where the robotic arms reload the shaft ready for the next cycle.
The advanced recipe driven OMRON control system with user-friendly HMI stores all the slitting operations including; meterage, number of cycles, operating speeds, unwind tension, rewinding parameters, lay-on-roller pressure & minimum gap distance, tab application, along with a direct modem link for immediate factory intervention.