Guidolin Girotto
RO Series Laser Die Cutting Systems
Guidolin Girotto’s RO Series galvanometer (galvo) laser die cutting & converting systems have revolutionized the way converters and application specialists conduct their manufacturing processes.
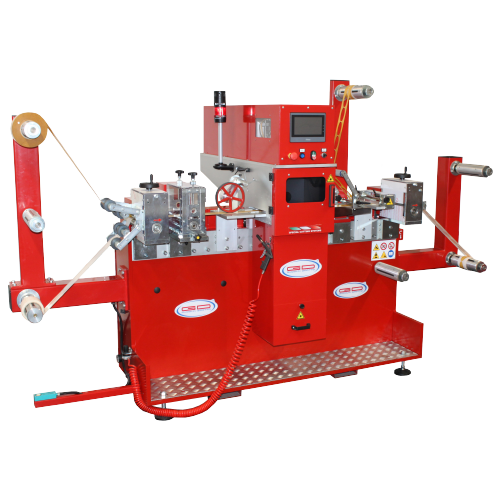
Guidolin Girotto’s RO Series galvanometer (galvo) laser die cutting & converting systems have revolutionized the way converters and application specialists conduct their manufacturing processes. Laser Cutting is the ideal digital (no hard tooling) cutting solution for prototypes, just-in-time manufacturing & short-medium production runs and is well suited for converting high accuracy components from flexible materials including label stock & PSA, double sided tapes, transfer tapes, foam tapes, gaskets, plastics, textiles, difficult abrasive materials & even aggressive adhesive materials like VHB that typically adhere to the cutting blade.
Innovative laser technology is being used more and more frequently in the converting market, both for prototyping and for production. Knowledge of these production methods, and the materials to be converted, is indispensable if the customer is to be provided with correct solution for their applications & requirements. Guidolin Girotto has partnered with the world’s leading manufacturers of industrial CO2 Lasers; recognized as leaders in the development of sealed CO2 lasers and electro-optic technologies. Sharing similar philosophies – to engineer and manufacture a range of high technology products that are easy to operate, reliable and affordable – thereby opening new applications for CO2 laser die cutting technology worldwide.
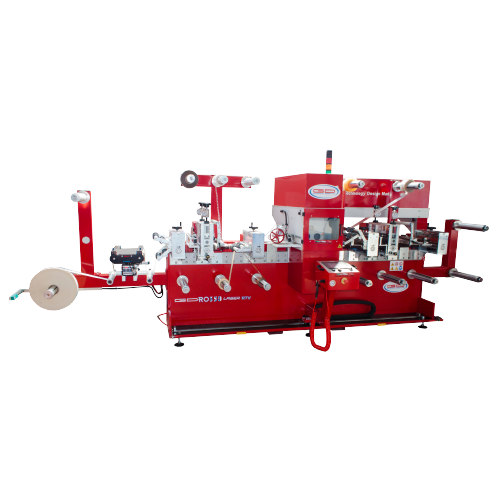
Guidolin Laser Die Cutting System Options
RO 175 EL – The RO EL Series is a cost-effective, entry level laser die cutting solution with a 175mm wide useful working width, engineered for processing a wide variety of materials including labels, adhesive tapes, double sided adhesives, VHB, textiles, paper, foam & rubber, silicone, PU, PE, PET, polycarbonates, polyethylene, polypropylene, abrasives and similar products.
RO 250 – The RO 250 model has a useful working width of 250mm and is the ideal solution for convertersthat demand versatility. This solution combines our traditional RO series rotary converting platform with the Laser Cutting module. The system interchangeability is the distinctive trademark of the Guidolin product and this unique design allows new systems to be installed on the machine without modifying the original set-up. “Multiple solutions in one machine.”
RO 350 – The RO 350 series offers the most flexibility and production through-put for materials up to 350mm in width. Depending on the application, the speeds of the RO 350 can reach 100 Mts/Min and the standard 350W RF “Self-Refilling” laser source is a highly-efficient CO2 laser ideal for applications on adhesives, plastics, graphics, overlays, labels and similar materials.
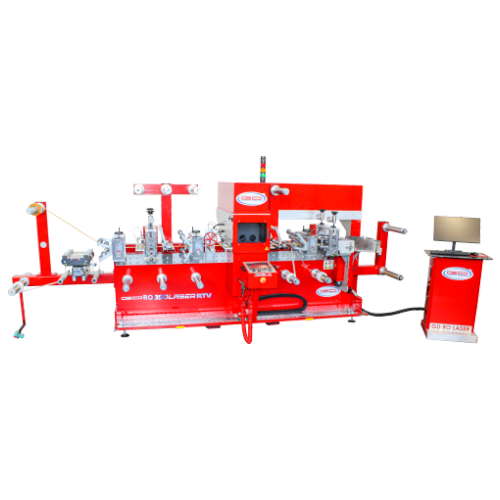
Laser Cutting – The Technological Advantage
Laser Cutting is an advantageous technology choice for cutting & converting a wide variety of materials for multiple sectors. Laser cutting is above all, precise, clean and silent. Laser cutting process utilizes laser energy to modify the shape of a product which results in the complete separation of the material. Guidolin Girotto’s careful evaluation of the features of the most suitable laser cutting systems grants optimum results for the reduction of time to market & an increase of production quality & capabilities.
Digital laser processing is capable of producing an infinite number of part dimensions; micro-parts and micro-perforations that other cutting technologies simply cannot achieve. Laser cutting also eliminates adhesive flow associated with aggressive double coated adhesive tapes since the beam virtually vaporizes the material in the laser path. By vaporizing the material, laser cutting prevents cut parts from bonding back together; where mechanical die cutting only displaces the substrate. The laser beam is concentrated on a very small spot (0.05-0.21mm) and exerts zero pressure on the component allowing the material to keep its original shape.
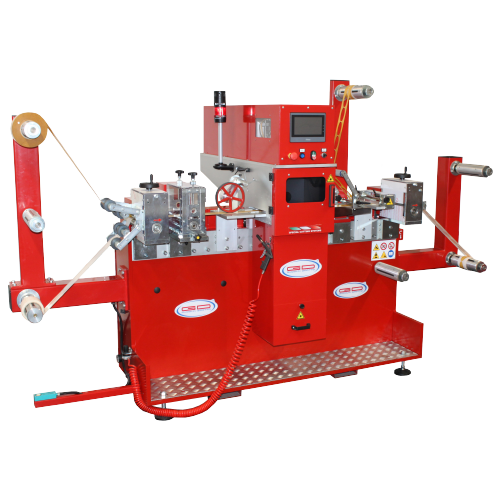
Types of Laser Cutting Processes
Ablation of Material – Material ablation is a process that virtually removes the material completely from the top to the bottom of the surface or partially from the top of the material to a pre-set specified depth. Typically, laser ablation refers to removing material with a pulse laser, but it is possible to ablate material with a continuous wave laser beam of the wattage (power) of the laser is high enough.
Laser Die Cutting – Laser die cutting is the complete removal and separation of the material from the top surface to the bottom surface along a designated path generated by the CNC or G-Code of the pattern to be cut. The focused laser beam is directed at the material, which then either melts, burns or vaporizes away leaving an edge with a high-quality surface finish. Laser die cutting can also include processes like kiss-cutting, slitting, perforation, through-cuts and/or slug removal.
Laser Engraving – Laser engraving is the process by which material is removed from the top surface down to a specified depth. By continuously varying the laser power, laser engraving can be used for textures, images, bar-codes, text and numbers.
Laser Marking – Laser marking, which is essentially engraving the material, is a broader category of methods to leave marks on an object to produce a readable identification or information such as a barcode, lot code, serial number or a part number. This technique does not involve the use of inks, nor does it involve tooling which contact the engraving surface & eventually wear out, giving it a significant advantage over alternative engraving or marking technologies where inks or tools have to replaced regularly.
Combined Processes – Digital laser processing is a proven, viable solution for processing a wide variety of materials. The multiple processes referenced above can be combined to total cut, kiss-cut and engrave/mark various substrates in roll or sheet form in both continuous, start-stop and tracking modes.