RFS CO.
DIE CUTTING & HEAT SEAL PRESSES
The RFS Comec Hydraulic Up-Stroke Heated Platen & Cutting Presses are versatile machines able to support total cutting & kiss-cutting, crease/seal applications, molding & trimming for a wide range of products; both natural & synthetic.
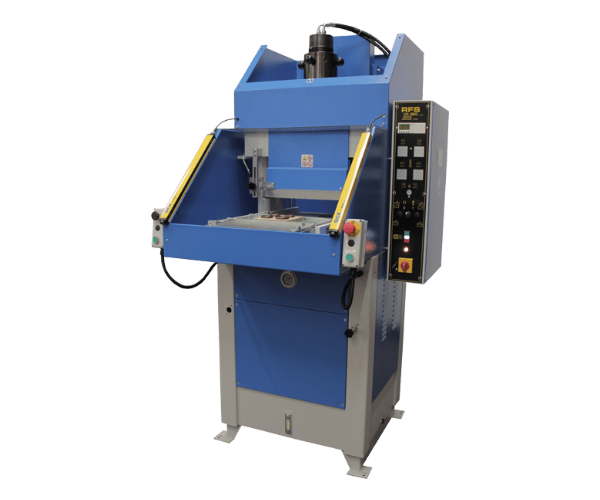
RFS Comec Die Cutting & Heat Seal Presses
The RFS Comec Hydraulic Up-Stroke Heated Platen & Cutting Presses are versatile machines able to support total cutting & kiss-cutting, crease/seal applications, molding & trimming for a wide range of products; both natural & synthetic. Ideally suited for textiles & non-woven materials, foams & synthetic fibers used for insulation & sound dampening properties, vacuum formed plastics, blister packaging, pre-printed graphics, laminated materials, leather & many more.
The RFS hydraulic up-stroke heated platen & cutting presses are designed, engineered & assembled in Vigevano Italy & can be customized to meet the customer’s individual production requirements with various transport feeding & handling systems to accommodate roll good materials. The minimum dimension of the working platen is 350mm x 300mm up to a maximum of 1200mm x 100mm – custom sizes available – with cutting powers up to 330 Tons. Platen dimensions, cutting power, dwell time, heat specifications (top & bottom) along with the level of the control software are critical components to maximize your manufacturing process.
The adjustment of the die cut is controlled via the PLC + Touchscreen with the following confirmed: 1) Automatic detection of the die height, 2) Electronic confirmation of cut depth & 3) Proportional valve to check pressure on the PLC. The upper and lower heated platens are controlled by 3 independent temperature regulators, or three independent zones, for precise temperature control. Pressure, controlled heat and dwell time are the key elements that make the RFS line of hydraulic die cutting presses the leaders in the industry.
The automatic operated sliding work table, with single push-button start, allows unobstructed loading and unloading of the materials. Available accessories include an automatic pad shifting device mounted to either the top or bottom platen for a clean cut every cycle, adjustable die rail supports so various die board widths and thicknesses can be utilized, dual tray configuration for increased production throughput, and customized photocell barriers to accommodate automatic loading & unloading robots in cell based manufacturing environments.
Die Cut Heat Seal Production
The RFS Heated Platen Press can be equipped with top and/or bottom heated platen depending on the application & individual requirements. The electrically heated platens provide uniform heat distribution & precise temperature control across the entire platen surface. Temperature accuracy can be monitored & controlled with a simple single zone controller or a more precise multi-zone system for increased temperature consistency throughout the entire platen area.
The standard RFS Hydraulic Heated Platen Presses have a maximum operating temperature of 199° C / 390° F. The standard CE electrically heated platen is equipped with round cartridge heaters & normally used in higher temperature or vacuum applications. These types of heated platens are insulated to maintain uniform temperature & the platen heaters are specially coated to improve heat transfer and ease of removal. Insert heaters provide efficient energy usage & rapid heat up & recovery times coupled with higher temperature capabilities with lower maintenance when compared to hot oil systems.
Ideal applications for a heated platen press include various textiles, synthetic fibers or non-woven materials used for sound dampening in the transportation industry (die cut, crease/seal), compression molding for a variety of foam materials, laminating & embossing operations, filter media in multiple layers, medical inflatables, packaging closures, life preservers and similar applications.
Typical tooling used for thermal sealing & cutting these types of products include traditional wood or metal based steel rule dies, or when higher quality sealing is necessary, the tool base can be manufactured with aluminum & brass materials to provide an even foundation for transferring heat to the rule which results in a better quality sealing on the final part. Thermal seal dies can be equipped with cutting blades and internal punches allowing forming and cutting to occur in the same cycle. The tool is mounted to an adjustable die rail support for greater flexibility when various size die boards are utilized.
Compact, highly versatile and robust with an efficient manufacturing foot print, it is ideal for cell based manufacturing processes.